A gravel bike to shred trails with: a review of the new Argonaut Cycles GR3
No eyelets, no suspension, pure speed. This capable featherweight race machine impressed
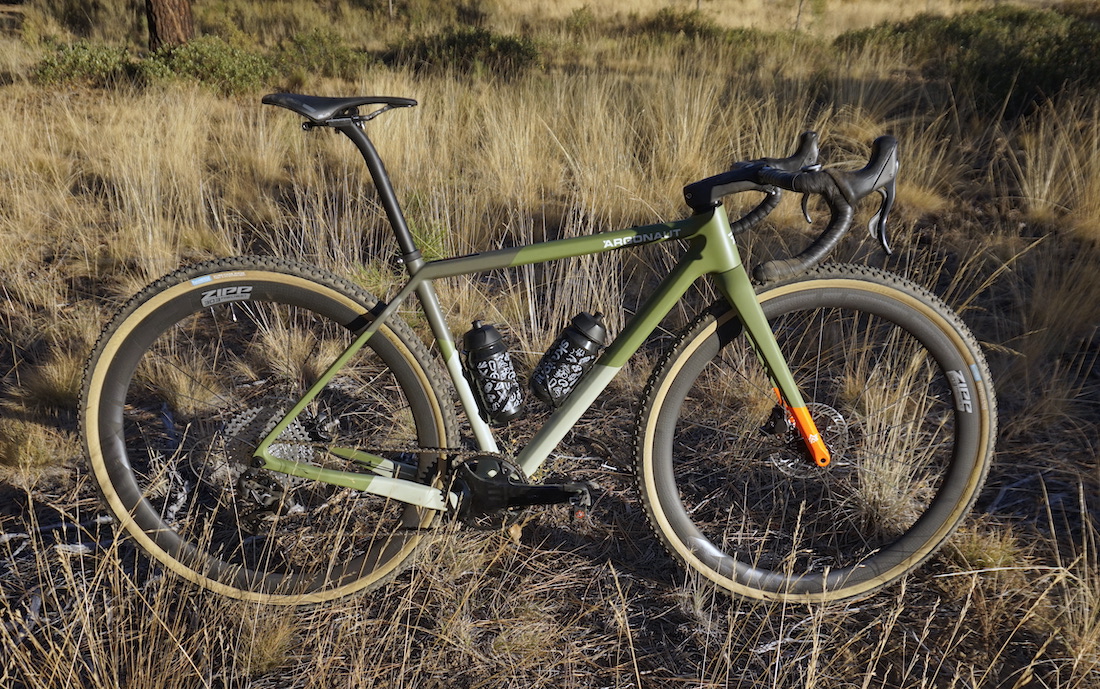
With room for 50c tires and a very slack front end, paired with responsive short rear triangle, the word ‘capable’ in case of the GR3 means being able to go anywhere, and do so while stomping on the pedals and going fast. Up a hill or zig-zagging through trees, this bike has the personality of a young border collie: energetic, fast and playful.
-
+
Lively
-
+
Lightweight
-
+
Great combination of capability and responsiveness
-
+
Climbs and handles well
-
+
Good value for a fully custom carbon bike
-
-
No fender mounts!
You can trust Cycling Weekly.
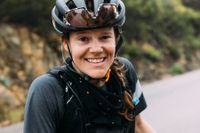
The mythical Argonauts were a band of heroes who accompanied their leader, Jason, on his seemingly impossible quest to find and capture the golden-woolled ram and return its Golden Fleece to the city of Lolcus so Jason could reclaim his rightful throne.
Together with his crew of Argonauts, Jason slayed monsters and giants, outsmarted sirens, and persevered through storms and many battles. The tale of Jason and the Argonauts was an unusual one for its time in that it celebrates the hero as much as the help he received along the way. Jason could not accomplish his great feat without his Argonauts and likewise, us cyclists cannot perform without our trusty and capable steeds.
At Argonaut Cycles in Bend, Oregon, Ben Farver and his team of craftspeople are on a quest as well. Not in search of the Golden Fleece, but in search of the edge of what is possible in custom bike design. Their tale is one of slaying industry standards and breaking free of the moulds of what’s been done as they seek to produce the world’s best custom carbon bicycles.
Carbon Done Differently
Argonaut founder Ben Farver explains the
Farver started building custom bikes for people back in 2007. And he, like so many of his contemporaries, turned to steel and its superior ride quality.
However, frustrated by the similarities of all those handbuild steel bikes that flooded the market, Farver looked to carbon to push not only his boundaries as a builder but also to push beyond the limitation of steel. Carbon offered nearly limitless potential for customization while also being lighter and stiffer than steel.
Feeling stymied by having to relinquish the machining, time frame and other parts of the process to third party manufacturing companies, he decided that in order to create the best possible product, he had to bring everything in house.
“I wanted everything in house for control of process and repeatability. Nobody builds our bikes better than we do,” Farver said.
These days, the designing, manufacturing, assembling and painting of every bike, one at a time, now happens —mostly by hand— under two roofs, in Bend, Oregon.
Custom all the way
Argonaut builds around 200 frames per year, and only one frame at a time.
Geometry and paint are just part of it, Farver says. Just like his steel frames in the early days, it’s the ride feel that is at the center of Argonaut’s work. The bikes, therefore, are customizable down to the individual carbon fibers.
“We tailor the carbon layup, the stiffness, of each part of our bikes to the individual customer,” Farver says.
It starts with the customer’s height, weight and even power numbers if available.
“I look at functional threshold power and one minute and three minute power, so I can understand how much torsional flex and how much force is going through the frame,” Farver explains. “ Then I look at their biking history, where they ride, what kind of roads, if it’s hilly or flat, and what other bikes they’ve ridden in the past and really enjoyed.”
Over the years, Farver created four rider case studies and concocted special stiffness recipes around them. These recipes serve as a starting point for many frame designs. Using the customer’s data, he can then tweak the stiffness numbers to ensure the frame flexes appropriately for the individual rider.
An overbuilt bike will feel dead and lifeless, Farver explains. Likewise, a frame that flexes too much is inefficient and will feel noodle-y.
Once designed, it’s off to manufacturing, which is very much Argonaut’s own.
Argonaut’s patented High Pressure Silicone Molding manufacturing process
Argonaut founder Ben Farver explains their patented High Pressure Silicone Molding manufacturing process
Beyond the carbon layup experimentations, Farver spent quite a few years testing the various manufacturing processes.
In general terms, carbon fiber frames and components are made using carbon fiber cloth and resin. Small, unique shapes are cut out of the carbon fiber cloths and, oftentimes, impregnated with resin, which acts as an adhesive, before being painstakingly placed in a mold. The pieces are then pressed together, most commonly with an inflatable latex bladder, and then cured in an oven.
While commonplace in the industry, the bladder approach can cause problems. As the bladder expands, there can be movement in the carbon pieces, causing fiber distortion or gaps in between the laminates. This means wrinkles, gaps that need to be filled and a potential inconsistency in how and where the frame flexes.
Argonaut’s patented process instead uses silicone wrapped alloy mandrels, which are machined in house and unique to every customer’s geometry. Carbon fibers are laid up by hand around the mandrels and then placed inside the mold. In the oven, these mandrels increase the pressure inside the mold, which is controlled by the amount of silicone wrapped around the mandrel’s skeleton.
O-rings surround the part being cured and seal the mold, keeping resin trapped into the system and internal pressures high. Once the mandrels are broken up and removed, the resulting frame is consistently smooth and, Argonaut argues, free of flaws.
“Our scrap and reject rate is 1-2 percent, which is super low,” Farver said.
Straight out of the mold, the surface finish is so clean that many of the Argonaut frames sport a full or partial clear coat so the neatness of the fibers can be seen.
Introducing the GR3
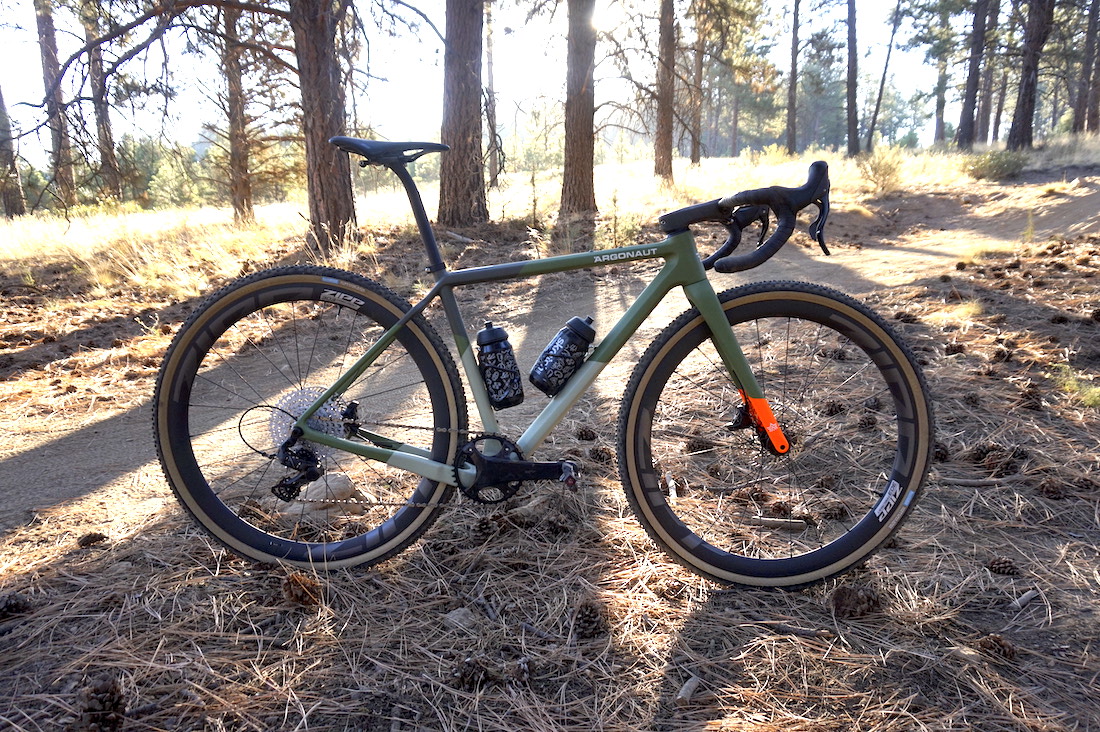
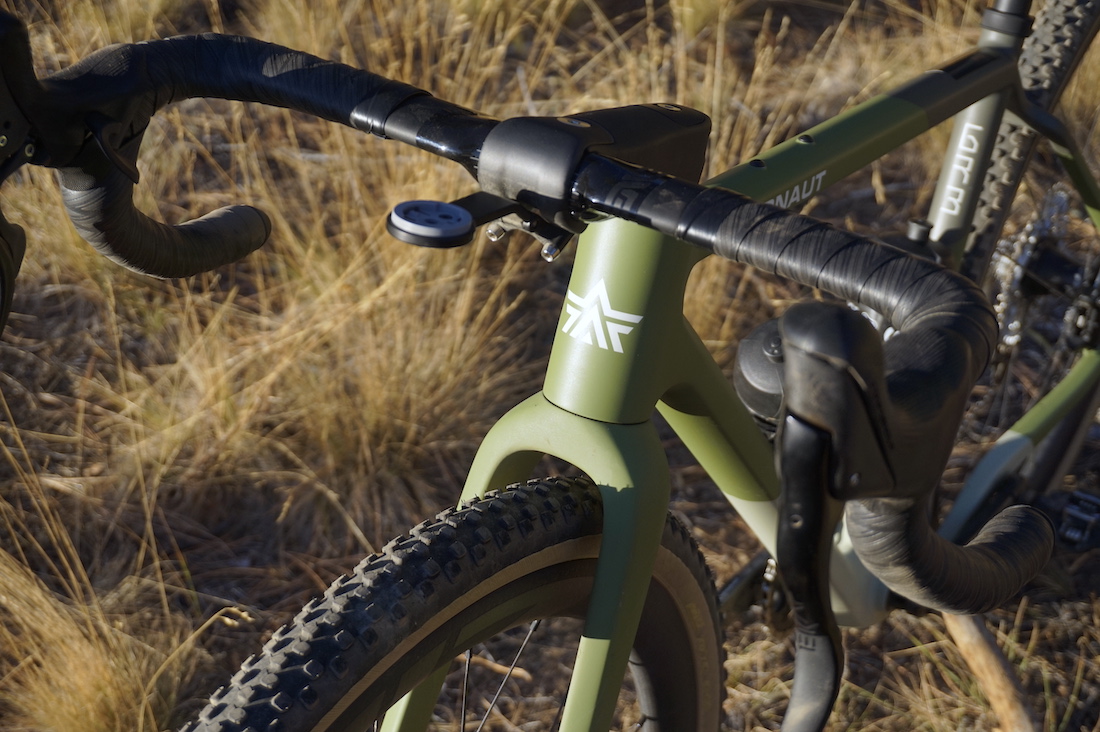
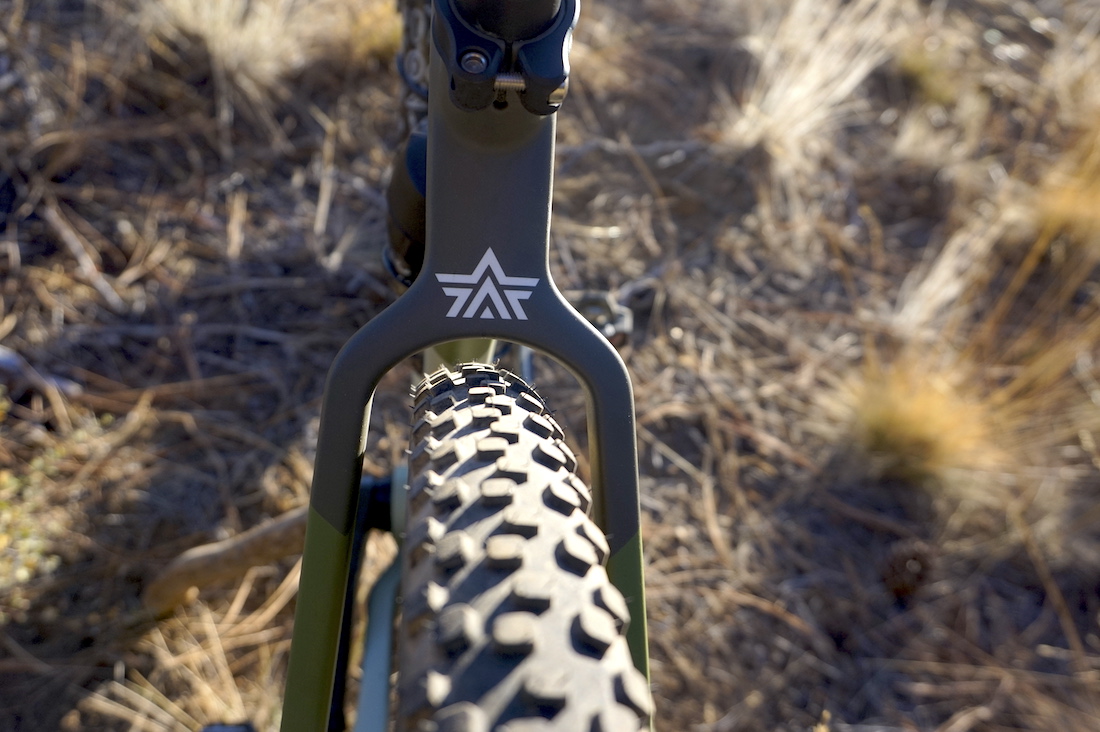
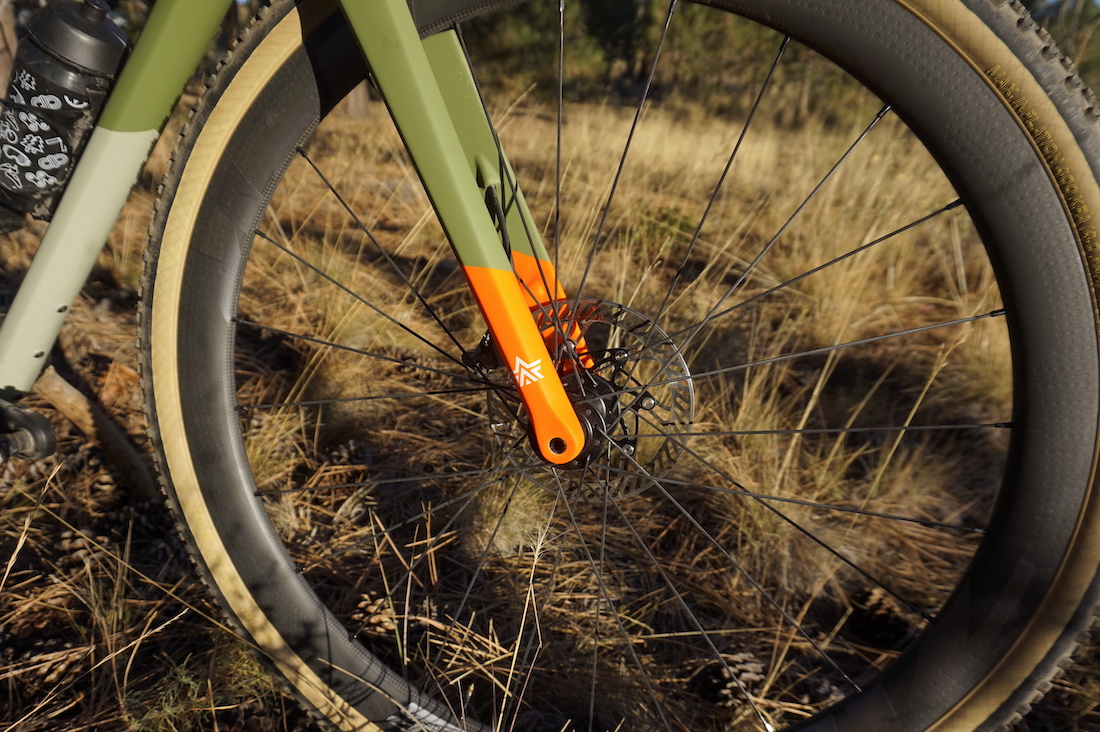
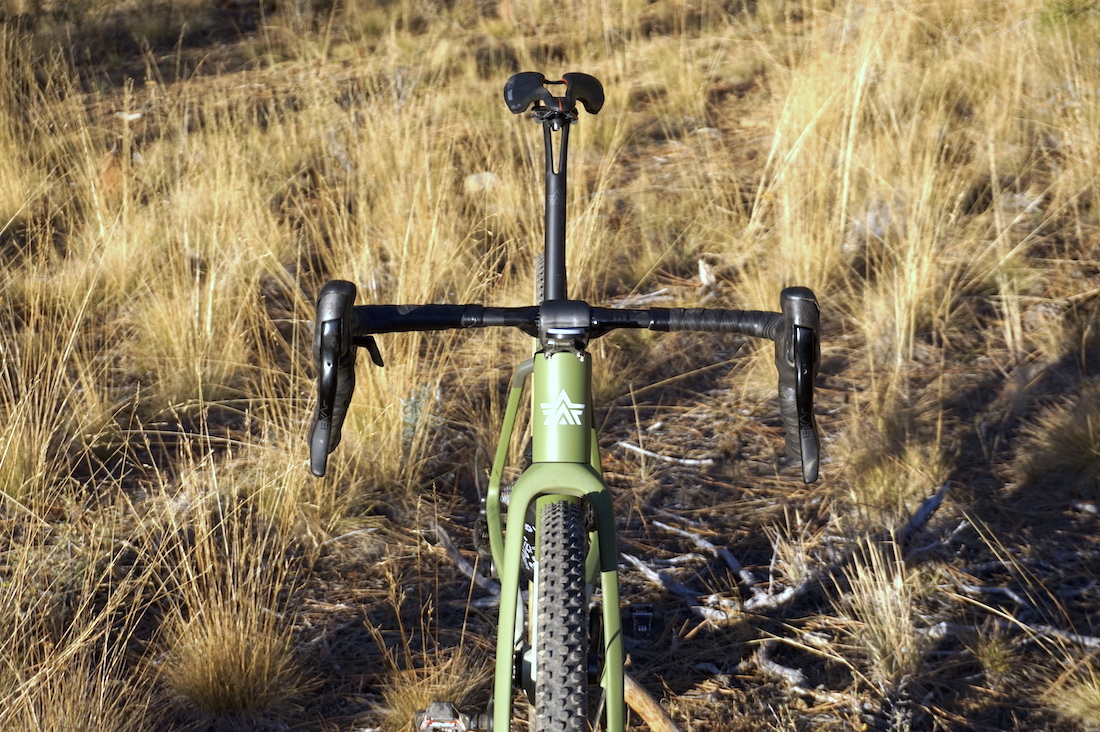
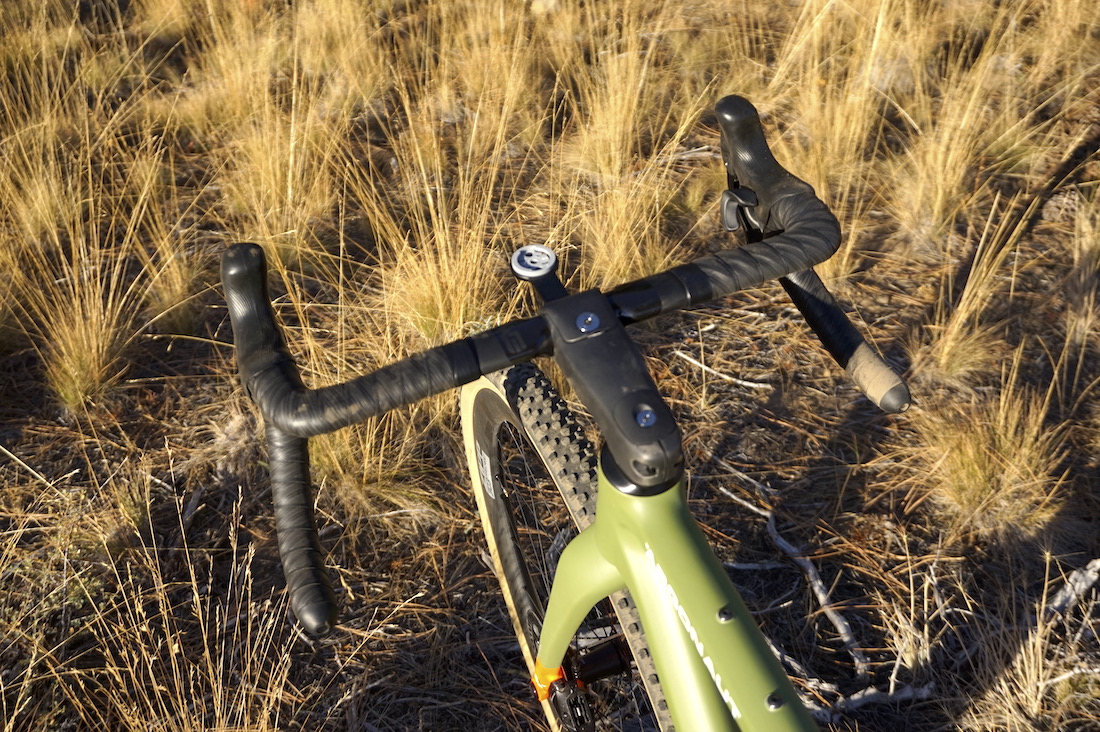
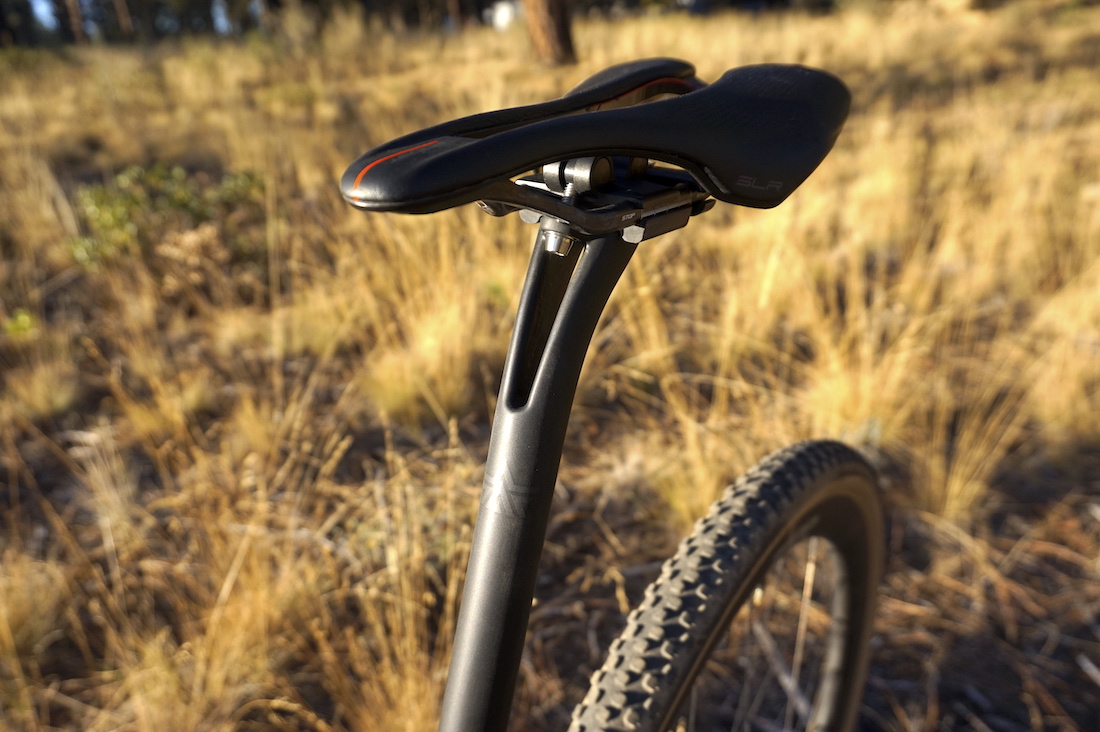
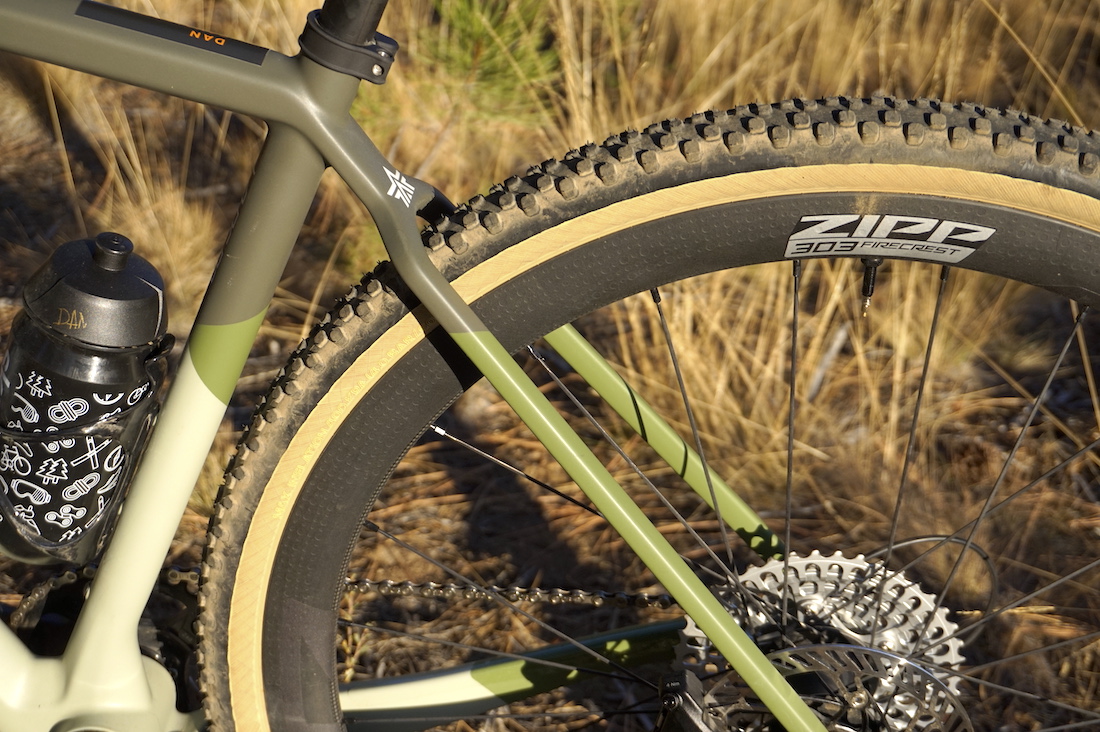
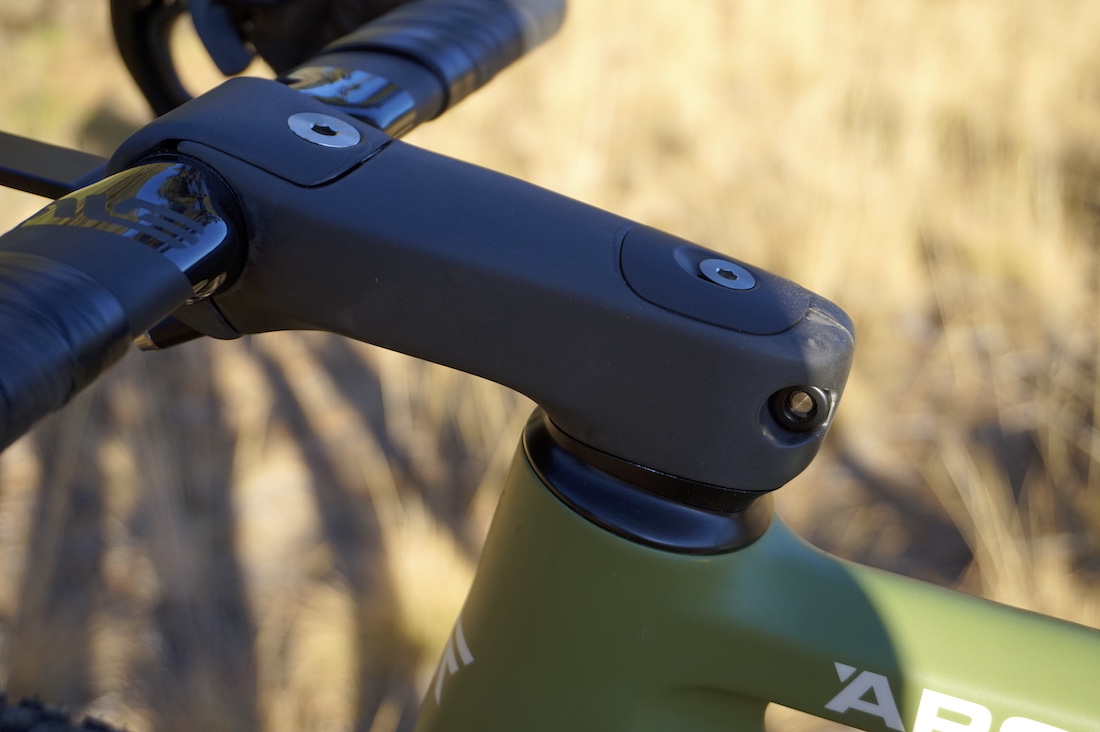
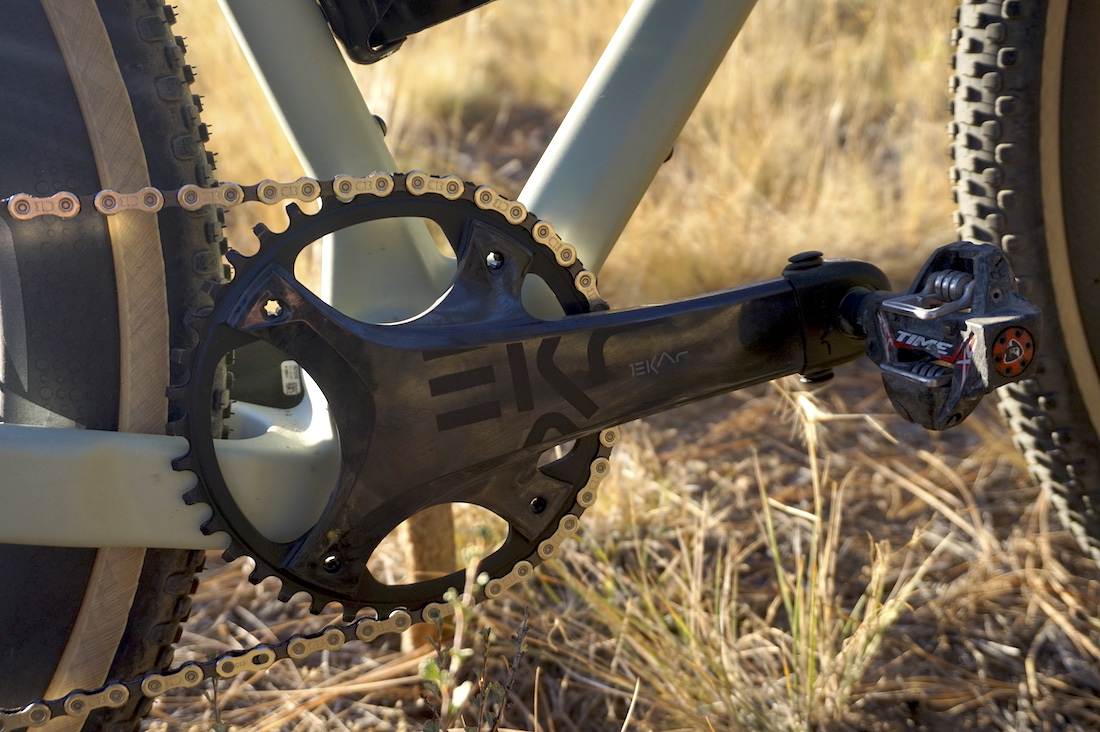
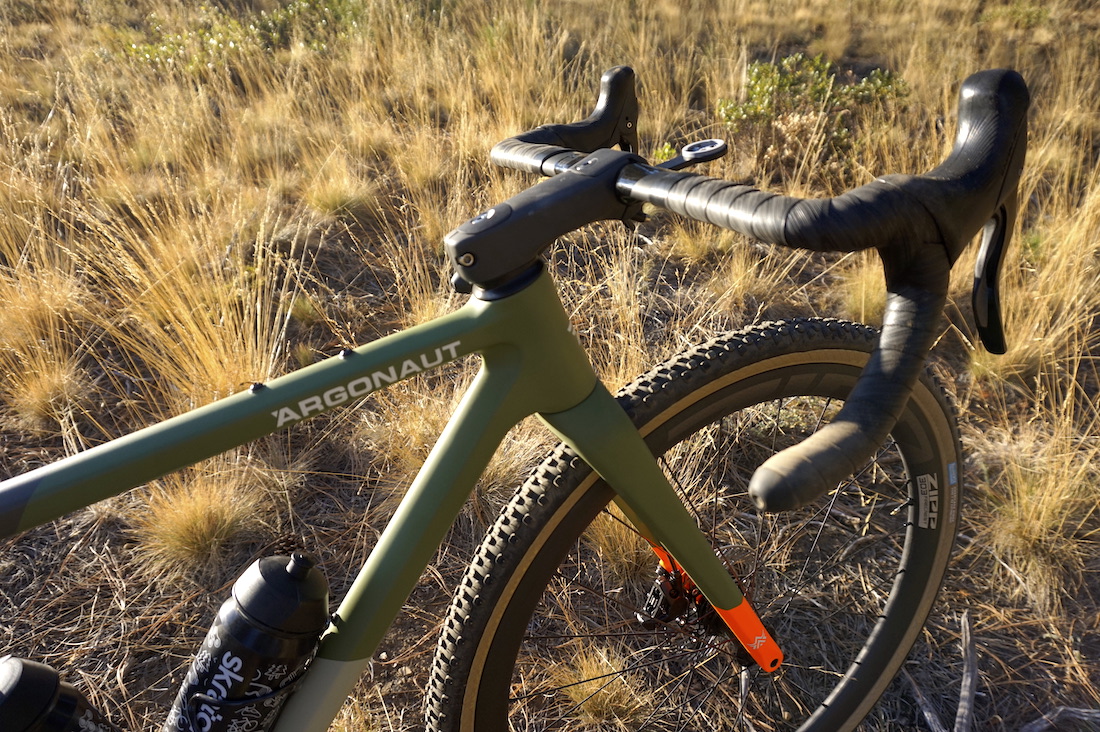
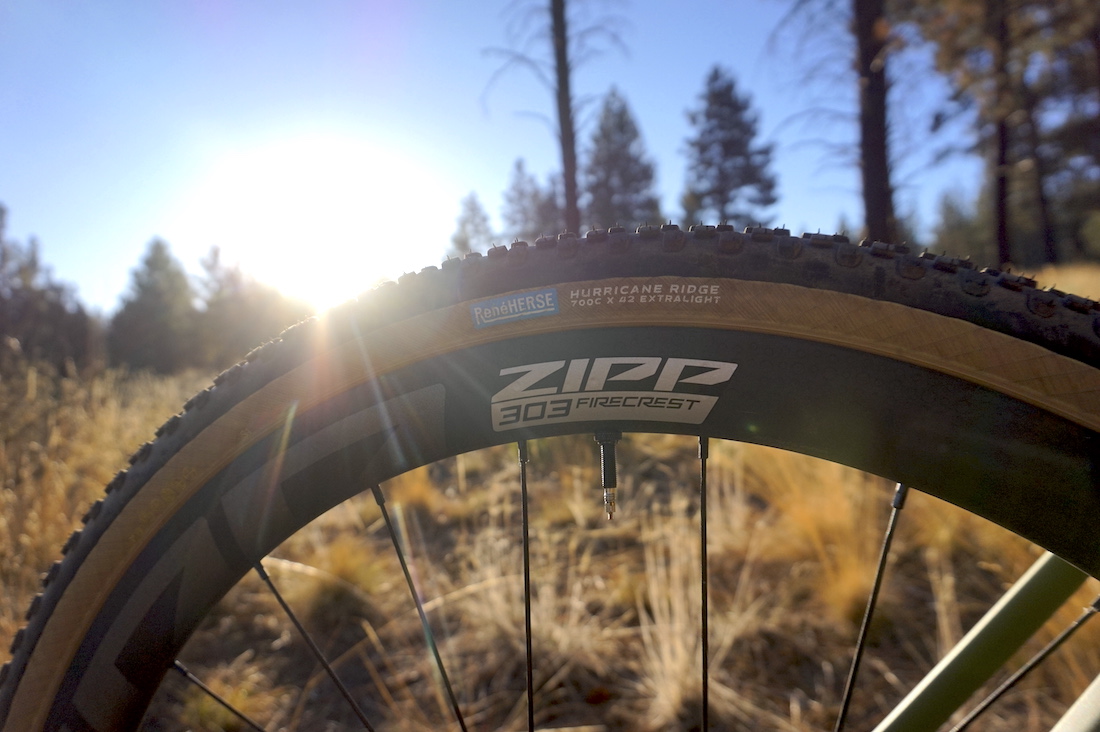
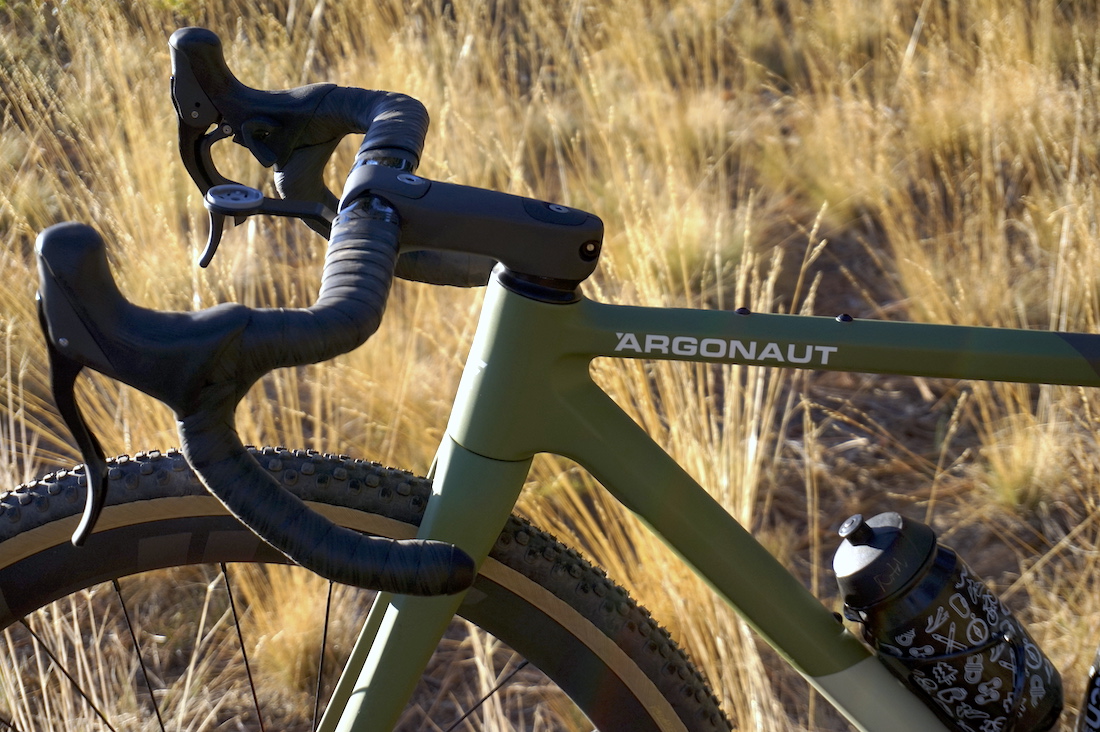
Launched today, Argonaut’s GR3 —Gravel Racer Three— features an all-new geometry meant to suit the “modern gravel cyclist” and to improve upon the areas in which the previous models were lacking.
“The GR2 felt undergunned,” Farver says. “I wanted to create a bike that climbs really well and accelerates really well and is really lively. But also one so you can bomb down and go downhill as fast as possible.”
The GR3 therefore is defined as a “clash of a full-on enduro bike with a pure roadie, blurring the edge of what a refined custom gravel machine is capable of.”
To achieve this combination, Farver paired a really slack front end and a lower bottom bracket with a short rear triangle. All while making room for 50c tires.
“To get more clearance, everyone has gotten into the habit of having really long chain stays because they think you need that for stability and for the extra clearance without having to get creative with the geometry. But all that does is make the bike feel sluggish,” Farver explains.
It took three years of design, research and testing, but the GR3 is the “perfect bike for riding and racing we like to do around here,’ Farver says, which includes fast roads, smooth and rough gravel, sandy cinder trails and plenty of singletrack.
The GR3 at a Glance
- Slack front end: A 57mm rake paired with a 68.5mm head tube angle make for a slack front end intended to provide control and stability when descending at speed
- Short Chainstay: A 415mm chainstays is meant to keep the snap alive in sprints and up a climb.
- A lower bottom bracket: The 75mm drop allows for more stability and tire clearance up to 50c tires.
- Sloped Top Tube: Meant to lower the center of gravity for better handling.
- Carbon layup: Argonaut opted to use standard modulus carbon for their customer-specific layup patterns instead of high modulus in favor of durability over years of rough and abusive nature of off-road riding.
- Internal Cable Routing for clean cockpits and easier attachment of handlebar bags.
- Argonaut Stem: The frameset comes with an Argonaut stem which was designed in-house for stiffness, durability and fully internal cable routing.
- Weight: The test bike, built with Campagnolo Ekar, Zipp 303 wheels and Rene Herse Hurricane Ridge tires weighed a claimed 16.8lbs.
- Price: Framesets (fork, stem, frame) are $6500 and pricing for the full builds will differ.
- Availability: Current build time is four months from the order date. Bikes are available customer direct in the U.S. or via the Service Course in the U.K. and Europe
How it Rides
The Argonaut crew sure knows how to have a rowdy good time. Bend is a bit of a mountain bike mecca here in the Pacific Northwest and they were not shy about taking us journalists on the vast network of singletrack trails as well as the more traditional gravel roads.
Over the course of three days, we rode rutty singletrack, sandy cinder roads, expansive gravel and fast pavement. In other words, everything this bike was meant to tackle and more.
As someone who loves underbiking, I’ve always said that the perfect Bend bike is a hardtail or a cyclocross bike. And so, by blending the two, Argonaut may just have created a unicorn.
Understandably, Argonaut wasn’t going to produce custom bikes for all of us journalists for a mere couple of days of riding. So instead, we were asked for our measurements and data beforehand and Argonaut then matched us with one of Farver’s four case studies and paired the frame with a stem, handlebar width and saddle to our preference.
While the ride feel wasn’t going to be as personally optimized as what Argonaut customers experience, Farver expected us to still get a sense of their base recipe and Argonaut’s known ride quality.
From the moment you swing a leg over the saddle, there's no denying that this is a race bike. It’s feathery light, snaps like a whip and begs to go fast.
It’s also stripped from any extras. There are no accessory mounts —not even fender eyelets—, no suspension or additional compliance, and with the internal cabling through the stem, the cockpit doesn’t even have any cables showing. It’s very much the opposite of a bikepacking, do-it-all gravel grinder. So if you’re looking to take this bike on overnight adventures, it may not be for you.
But while it may not be the n-1 bike so many gravel enthusiasts are gravitating toward, the GR3 interprets ‘capable’ differently.
With room for 50c tires and a very slack front end, paired with responsive short rear triangle, the word ‘capable’ in case of the GR3 means being able to go anywhere, and do so while stomping on the pedals and going fast. Up a hill or zig-zagging through trees, this bike has the personality of a young border collie: energetic, fast and playful.
I admit the front felt almost twitchy at first, but the handling of the GR3 soon brought a smile to my face. It’s actually quite dynamic. On the singletrack trails it cornered with ease and was confidence-inspiring on the descends. When the roads turned up or the pace increased, the bike responded promptly with my own (lack of) fitness being the only limiter.
Due to its featherweight, liveliness and fairly aero front end, the GR3 performed perfectly fine on the paved stretches, and I would imagine that with a set of slicks, this bike could double as a roadie as well.
My longest ride on the GR3 was just short of 70 miles so I cannot speak to the ultra long days in the saddle where riders are increasingly looking for comfort in suspension products, but even without the customized-to-my-needs carbon layup, the frame did a good job soaking up the bumps and rutts to where I could have gone longer.
Our test build came with Campagnolo’s Ekar group set and hyper-thin Enve bar, which matched the frame’s performance well. The bar paired with Argonaut’s stem allows for that clean, cable-free look. And with the frame’s encouragement to push the limits on the descents, the stopping power of the Campy brakes impressed.
The lack of accessories and aggressiveness of this bike may turn some folks away, but if you’re in the market for a lively racer, have a closer look.
At $6,500 for a fully custom frameset consisting of frame, fork and stem, I find the price tag quite reasonable, even. My educated guess puts you at $9,800 to $11,500 for a fully custom, fully carbon bike with high-end components. Yes, that’s a lot of money, no doubt. But it’s significantly less than an off-the-racks top-end Specialized Diverge STR ($14,000) or BMC Kaius ($12,000).
Thank you for reading 20 articles this month* Join now for unlimited access
Enjoy your first month for just £1 / $1 / €1
*Read 5 free articles per month without a subscription
Join now for unlimited access
Try first month for just £1 / $1 / €1
The latest race content, interviews, features, reviews and expert buying guides, direct to your inbox!
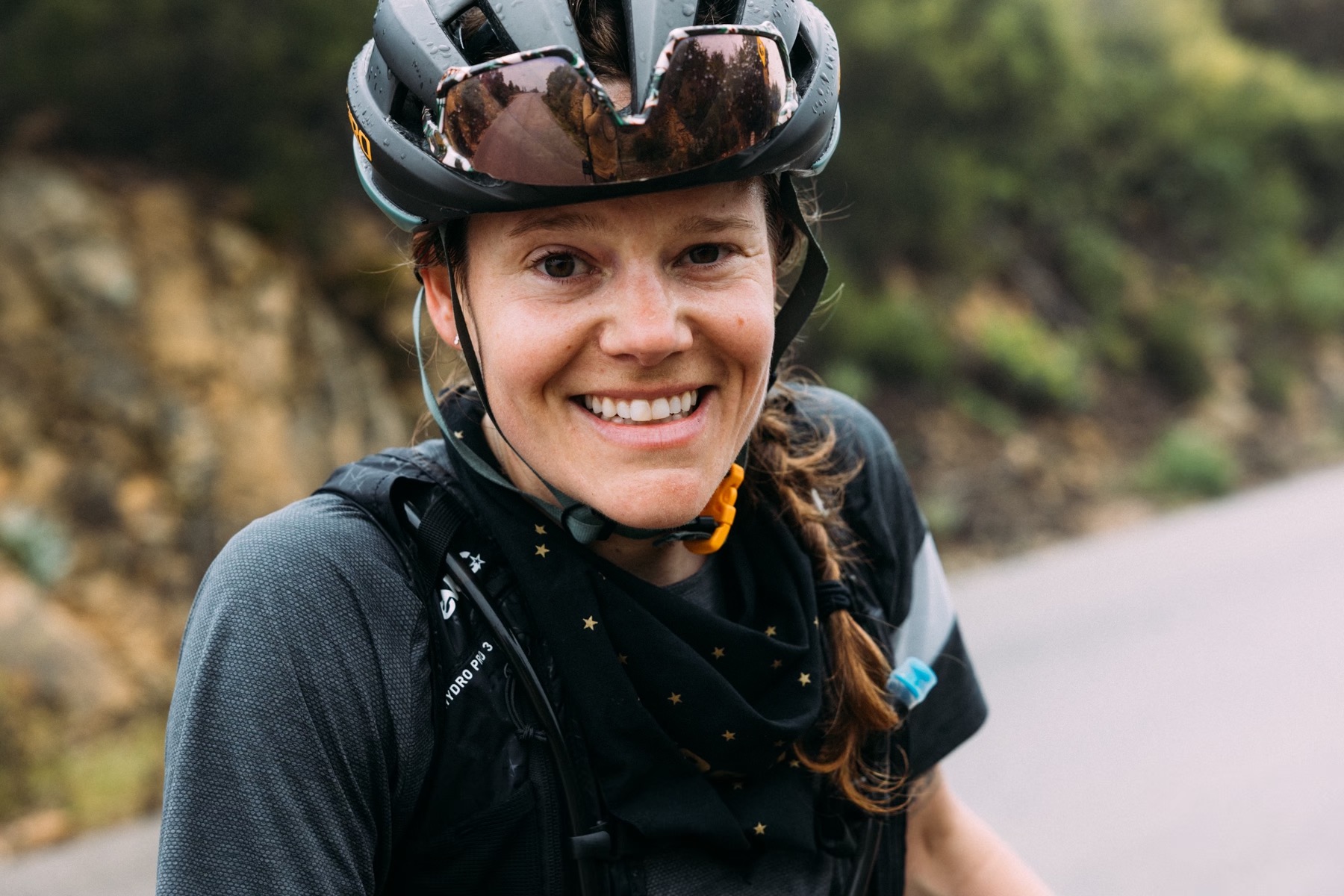
Cycling Weekly's North American Editor, Anne-Marije Rook is old school. She holds a degree in journalism and started out as a newspaper reporter — in print! She can even be seen bringing a pen and notepad to the press conference.
Originally from the Netherlands, she grew up a bike commuter and didn't find bike racing until her early twenties when living in Seattle, Washington. Strengthened by the many miles spent darting around Seattle's hilly streets on a steel single speed, Rook's progression in the sport was a quick one. As she competed at the elite level, her journalism career followed, and soon, she became a full-time cycling journalist. She's now been a journalist for two decades, including 12 years in cycling.