Carbon Done Differently: A Visit to Argonaut Cycles' Headquarters
We traveled to Bend, Oregon to see how these Made in the USA, uniquely custom, carbon steeds are crafted
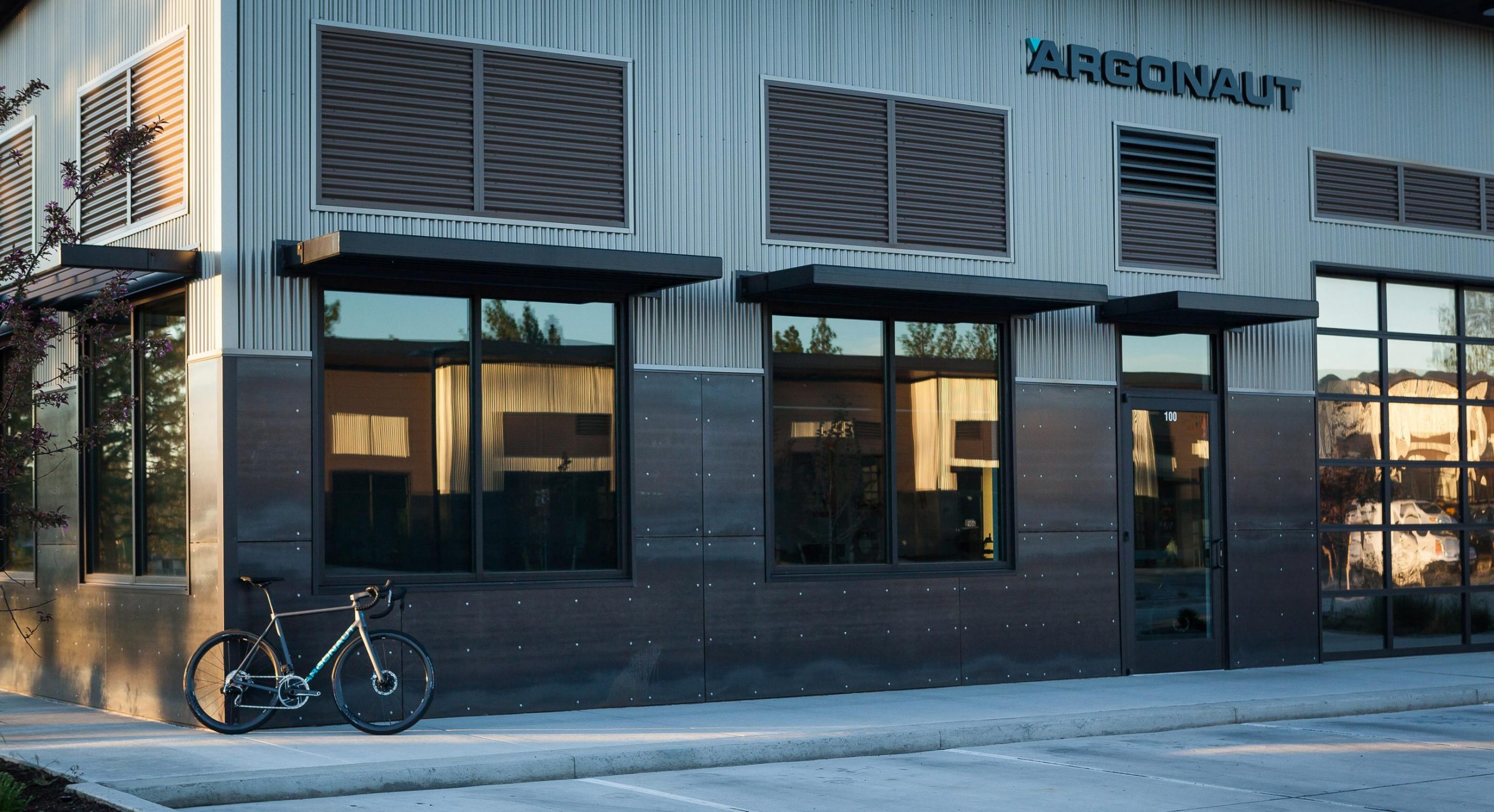
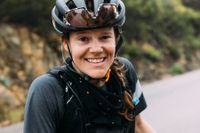
In the fall of 2022, Argonaut Cycles invited Cycling Weekly to come enjoy the last of the season's warm days on Bend's vast network of trails aboard their newest gravel racing machine, the GR3, and stop by their headquarters to see how their fully custom, Made in the USA carbon steeds are made.
Carbon Done Differently
Argonaut was founded by bike builder Ben Farver, who today is joined by 18 employees.
As part of the great Portland bike building boom of the late 'noughties', Farver started building custom bikes for people back in 2007. And he, like so many of his contemporaries, turned to steel and its superior ride quality.
However, frustrated by the similarities of all those handbuilt steel bikes that flooded the market, Farver looked to carbon to push not only his boundaries as a builder but also to push beyond the limitation of steel. Carbon offered nearly limitless potential for customization while also being lighter and stiffer than steel.
He initially worked with Innovative Composites Engineering (ICE) out of White Salmon, Washington, for the machining of his molds. But with ICE going after the growing aerospace market and Farver feeling stymied by having to relinquish the machining, time frame and other parts of the process to a third party, he decided to bring everything in house.
Ben Farver shows off his early steel frames
These days, the designing, manufacturing, assembling and painting of every bike, one at a time, now happens—mostly by hand—under two roofs, in Bend, Oregon.
“I wanted everything in house for control of process and repeatability. Nobody builds our bikes better than we do,” Farver said.
The latest race content, interviews, features, reviews and expert buying guides, direct to your inbox!
“By and large the bicycle industry is primarily made up of marketing companies where they have twice as many sales and marketing people as they do engineers. We are first and foremost a manufacturing and engineering company. Our intention is to make things and to make them as consistently and with as high a level of quality as possible, repeatedly.”
Farver says that it’s this absolute control of the process, paired with their patented High Pressure Silicone Molding manufacturing process and customization that results in what he believes to be the best bikes money can buy.
Custom all the way
Custom machined molds - one for each customer
Argonaut builds around 200 frames per year, and only one frame at a time.
Geometry and paint are just part of it, Farver says. Just like his steel frames in the early days, it’s the ride feel that is at the center of Argonaut’s work. The bikes, therefore, are customizable down to the individual carbon fibers.
“We tailor the carbon layup, the stiffness, of each part of our bikes to the individual customer,” Farver says.
It starts with the customer’s height, weight and even power numbers if available.
“I look at functional threshold power and one minute and three minute power, so I can understand how much torsional flex and how much force is going through the frame,” Farver explains. “ Then I look at their biking history, where they ride, what kind of roads, if it’s hilly or flat, and what other bikes they’ve ridden in the past and really enjoyed.”
The carbon layup is completely unique to each customer. Molds and tools are machines in-house for each rider.
Over the years, Farver created four rider case studies and concocted special stiffness recipes around them. These recipes serve as a starting point for many frame designs. Using the customer’s data, he can then tweak the stiffness numbers to ensure the frame flexes appropriately for the individual rider.
An overbuilt bike will feel dead and lifeless, Farver explains. Likewise, a frame that flexes too much is inefficient and will feel noodle-y.
Once designed, it’s off to manufacturing, which is very much Argonaut’s own.
Goodbye latex bladder, hello mandrels
A silicone wrapped mandrel
Beyond the carbon layup experimentations, Farver spent quite a few years testing the various manufacturing processes.
In general terms, carbon fiber frames and components are made using carbon fiber cloth and resin. Small, unique shapes are cut out of the carbon fiber cloths and, oftentimes, impregnated with resin, which acts as an adhesive, before being painstakingly placed in a mold. The pieces are then pressed together, most commonly with an inflatable latex bladder, and then cured in an oven.
A frame is placed in the oven to cure
While commonplace in the industry, the bladder approach can cause problems. As the bladder expands, there can be movement in the carbon pieces, causing fiber distortion or gaps in between the laminates. This means wrinkles, gaps that need to be filled and a potential inconsistency in how and where the frame flexes.
Argonaut’s patented process instead uses silicone wrapped alloy mandrels, which are machined in house and geometry specific. Carbon fibers are laid up by hand around the mandrels and then placed inside the mold.
Carbon fiber pieces are painstakingly folded around the mandrel by hand
In the oven, these mandrels increase the pressure inside the mold, which is controlled by the amount of silicone wrapped around the mandrel’s skeleton.
O-rings surround the part being cured and seal the mold, keeping resin trapped into the system and internal pressures high. Once the mandrels are broken up and removed, the resulting frame is consistently smooth and, Argonaut argues, free of flaws.
While the alloy mandrel skeletons can be reassembled for a new geometry, the silicone that's wrapped around them is a waste product — around 800-900 grams of silicone per frame.
The molds can be reused and Argonaut sells frames with both past and "proven" geometries as well as new and fully custom geometries. Farver says there's about a 60-50 split between proven geometries and new ones.
How clean is that frame right out of the mold?
Finishing touches
Argonaut makes its own stems and seatpost, and painting is done in-house as well. Before use any third part item like a fork or wheels, Argonaut conducts its own stress and failure testing. It conducts the same tests on its own products.
“Our scrap and reject rate is 1-2 percent, which is super low,” Farver said.
Straight out of the mold, the surface finish on the frames is so clean that many of the Argonaut frames sport a full or partial clear coat so the neatness of the fibers can be observed. Customers can, of course, opt for a paint scheme of their choosing. As with the rest of the process, the paintwork is done in-house.
The paint booth
The Finished Result
Custom Argonaut framesets consist of a frame, fork and Argonaut stem. Complete builds, featuring high-end carbon wheels and components from the industry's leading brands, start at $9400.
In the U.S., customers can order directly from the brand. In the U.K. and Europe, Service Course is the brand's main distributor.
The Argonaut G3 gravel racerBe
How does it ride? Be sure to check out our review of the all-new Argonaut GR3 gravel bike.
Thank you for reading 20 articles this month* Join now for unlimited access
Enjoy your first month for just £1 / $1 / €1
*Read 5 free articles per month without a subscription
Join now for unlimited access
Try first month for just £1 / $1 / €1
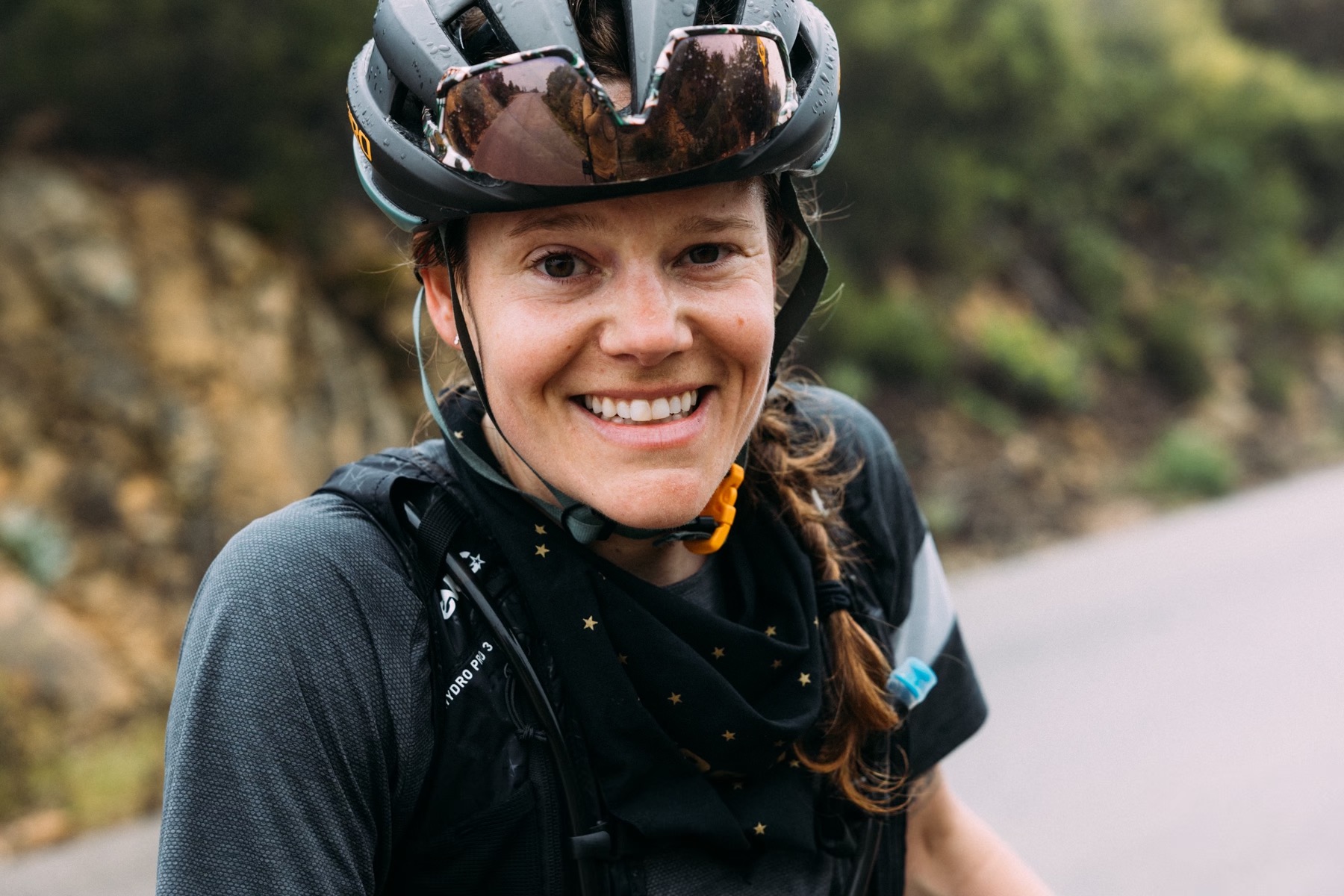
Cycling Weekly's North American Editor, Anne-Marije Rook is old school. She holds a degree in journalism and started out as a newspaper reporter — in print! She can even be seen bringing a pen and notepad to the press conference.
Originally from the Netherlands, she grew up a bike commuter and didn't find bike racing until her early twenties when living in Seattle, Washington. Strengthened by the many miles spent darting around Seattle's hilly streets on a steel single speed, Rook's progression in the sport was a quick one. As she competed at the elite level, her journalism career followed, and soon, she became a full-time cycling journalist. She's now been a journalist for two decades, including 12 years in cycling.