Hope's secret Olympic time trial bike didn't go to Tokyo but it will go into production next year
Cycling Weekly gets an exclusive look at the first prototype of the roadgoing Team GB Olympic track bike
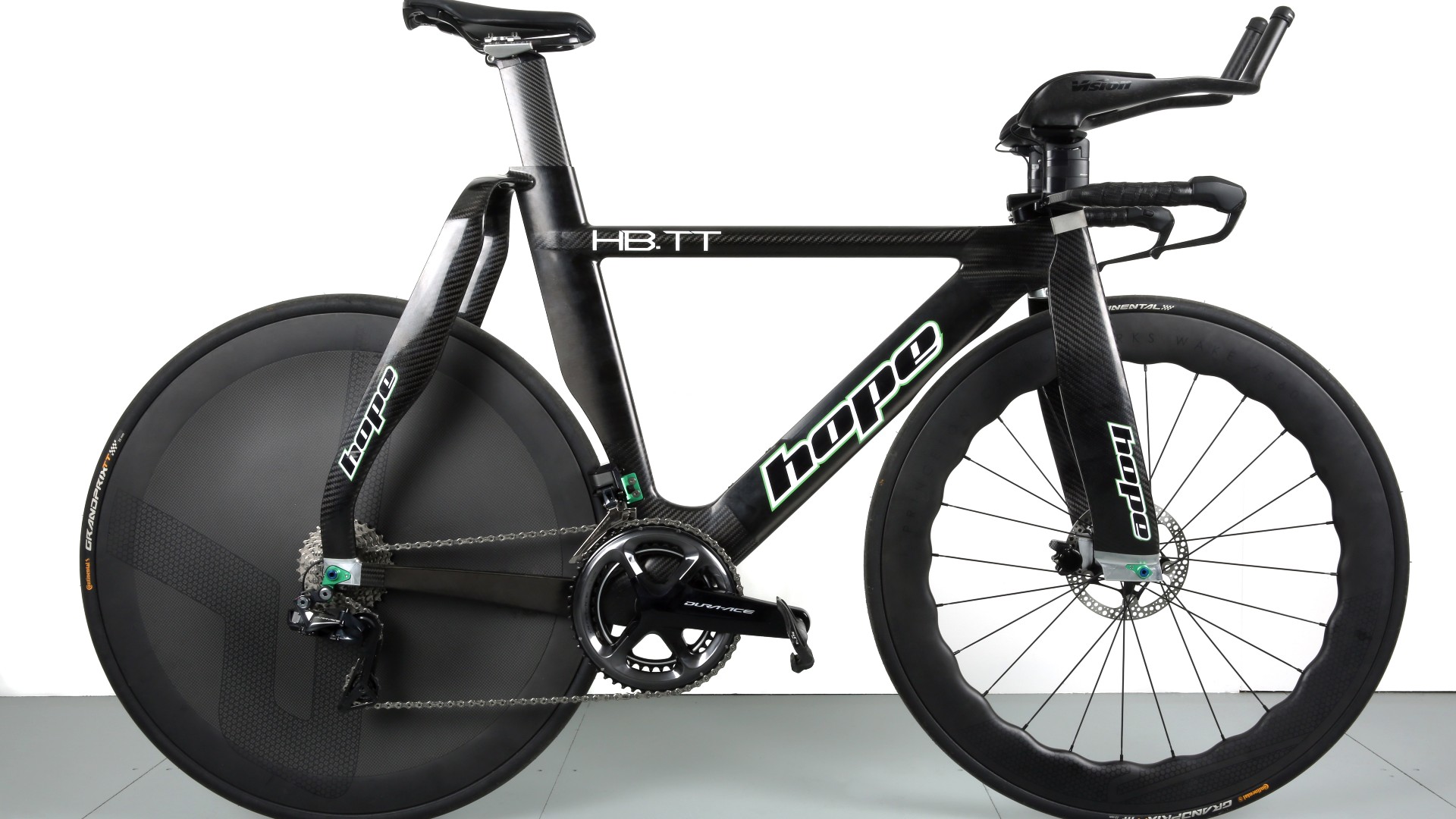
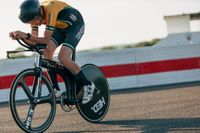
British brands Lotus Engineering and Hope Technology collaborated to develop and produce the already iconic Hope x Lotus HB.T bike that will be ridden in the Izu velodrome next week. But after the track bikes were finished and delivered to British Cycling, Hope decided to continue working on a road time trial version that would retain both the looks and the aerodynamics of the velodrome version with its radical arching 8cm-wide stays.
Hope gave Cycling Weekly an exclusive look at the first prototype, which they stressed is very much a work in progress - but nevertheless looks absolutely stunning.
“We were focused on the track but very quickly we thought, why not make a time trial bike and use the same advantages?” says Ian Weatherill, Hope Technology’s co-founder and managing director.
“We started working on it a year or so ago now. It would have been nice if we could have had it finished in time for Tokyo but we were concentrating so much on getting the track bike to British Cycling and the wheels as well. Originally we were plan B and then we became plan A, then they had no wheels either so we had to make the disc wheel and the tri-spoke. So we had a lot more work than we thought.”
Additionally, making a road version of the HB.T bike wasn’t quite as simple as just bolting some brakes and gears on it. The earlier UKSI track bike of the early 00s was adapted for the road, but its relatively conventional configuration didn’t present the same issues that Hope faced with the road version of the HB.T, which will be called HB.TT
Weatherill explains that even before the issues of fitting brakes and gears could be addressed, there was the fact that different forces go through a TT bike compared to a track bike. “The configuration is completely different for a time trial bike,” says Weatherill. “You think of a track sprinter - that changes the layup. It also changes things like the width of the chainstay.”
The team started by 3D modelling the bike, trying to keep the aerodynamics the same as the track bike. Then they worked on the bike being able to accommodate a front derailleur so that it could run a double chainring. “There’s a big climb in Tokyo and that’s why it needed the double chainring,” explains Weatherill. “We had to get chainline clearance right. Now we’re thinking, should we do the next version with a single chainring at the front because then we wouldn’t have to modify it as much. The one we’ve built is still very much a prototype.”
The latest race content, interviews, features, reviews and expert buying guides, direct to your inbox!
Integrating the Di2 and the hydraulic hoses was “quite a challenge” according to Weatherill. “The disc brake hose runs inside the fork and then you’ve got the dropouts that we’ve made especially to integrate the brake calipers,” says Weatherill.
However, there are still changes to be made to the bottom bracket height - it is still at track-bike height - and Hope is still making modifications to the brakes. “The caliper on the front is completely different from anything else,” Weatherill says. “But making the components ourselves we can make things especially.”
However, the bike is designed for a standard groupset and the prototype is fitted with a standard Shimano Dura-Ace crankset and uses regular Di2 shifting on Vision Metron tri-bar extensions.
Is it competitive compared to other leading time trial bikes?
“Of course on the track you have no yaw angles, no crosswinds, so we’ve got quite a bit of work to do. We’ve had a go in the wind tunnel and we’ve had lots of people playing around with it real-world testing it, time triallists testing it, riding it and giving us feedback. They’ve said it feels fantastic; they’re not sure yet whether it’s any faster. So to get it feeling right immediately is great, but we’ve got work to do with the disc brakes and the aerodynamics in those areas.”
Additionally, the prototype bike isn’t made with the high-grade carbon that the production versions will use, so it has some weight to lose.
“We have Chris Clarke who did the UKSI bike - he picks the carbon we’re going to use. The fibres are from Japan and then the actual material is made in the UK. It’s the same carbon that the track bikes use. We haven’t used the high grade carbon on the first prototype. We’ve just been working on it in the wind tunnel and been making it incredibly strong. The next step will be to put the high grade carbon into the frame to reduce the weight. The final version will be competitive compared to other carbon time trial bikes.”
The bike is also compatible with standard thru-axle road wheels: 12x100mm and 12x142mm but Weatherill says, as with the track bikes, Hope plans to produce time trial wheels too. The prototype is fitted with Princeton CarbonWorks Wake 6560 front wheel and a Princeton rear disc.
He foresees Hope carrying on improving the bike and moving away from the standard components from the big three groupset manufacturers: “I think we’ll gradually start producing our own levers as well,” says Weatherill. “That’s the thing with other people’s time trial bikes, they’re stuck with whatever SRAM or Shimano produce. The next step for us will be to take the componentry away from them, to start to do some different things.”
What exactly does he have in mind?
“Things like the lever blades and the master cylinders. Other bikes are stuck with Shimano or SRAM, quite a large lump. It’s a very niche market and you can understand why those brands don’t make something special. But for us, as it was years ago when we started doing our own disc brakes, niche suits us: 500 or 1,000 units is not a problem.”
Weatherill says the team are “not far off” getting the bike UCI legal. With the track bike already rubber-stamped, of course, he says the response from the UCI is “good”.
And there’s also a triathlon-specific version in the pipeline that could even appeal more to UK time triallists whose bikes don’t have to be UCI legal.
At the moment there’s just one mould that Weatherill says is somewhere between medium and large.
“It depends on the success and how well it’s received as to whether we’ll produce smaller and larger sizes,” says Weatherill. “Because we produce the moulds ourselves we’ll see how things go and if we get a bit of demand we’ll make smaller and larger sizes.”
Weatherill estimates that it takes Hope about a month to produce a new mould for a new frame size: “We’ve got the design, we machine it all and do the layup. That’s the thing about not going to Asia. The machine is next to the people who lay it up; sales are 100 metres away, they come down and say ‘I’ve got loads of people who want to buy a small bike, get one made,’ so that’s the flexibility of producing it in house.”
If the demand is there, Weatherill says Hope could make five or six HB.TT bikes a week, which is “a nice number for us”.
So how far away from going to market is the bike?
“Timescale wise we hope to have something to sell next year. There’s work to be done on the disc brakes to make them more aero and we’re taking a bit of help and advice on things like that, but you could place an order and it would fit in with the rest of the bike market, which is delivery some time next year.
And the price?
“We’d like to be competitive - something like £12-15,000. Not crazy. If we’re producing the things in house ourselves we could keep it sensible. That would include the wheels as well.”
One last question remains: what happened to the collaboration with Lotus? The Hope HB.TT doesn't feature the name of the legendary car company on its sleek carbon chassis?
“It’s no offence to any other companies, but we find it easier to do things ourselves,” says Weatherill. Collaborations are great but they can stifle things so it’s a lot easier if we do it all in house.
“We’ve produced our own fork now. The bike was made by us anyway - it was just the forks and the bars [that weren’t].
“Making the components ourselves we can make things specially. The bridges on the fork are all 3D machined out of aluminium. There are some very elaborate creations on there. We haven’t 3D printed any of the components - we can produce them faster because we’ve got the machines here and the know-how.
“When you’ve Lotus and Renishaw and British Cycling involved, they love titanium 3D printing but it’s so prohibitive on price and on time. Because we’re machinists we can produce something that’s only a few grams heavier and you can reproduce it, modify it, keep changing it.
“So now it’s a purely Hope bike. The design was a concept by British Cycling but British Cycling have nothing to do with this bike.”
Thank you for reading 20 articles this month* Join now for unlimited access
Enjoy your first month for just £1 / $1 / €1
*Read 5 free articles per month without a subscription
Join now for unlimited access
Try first month for just £1 / $1 / €1
Simon Smythe is a hugely experienced cycling tech writer, who has been writing for Cycling Weekly since 2003. Until recently he was our senior tech writer. In his cycling career Simon has mostly focused on time trialling with a national medal, a few open wins and his club's 30-mile record in his palmares. These days he spends most of his time testing road bikes, or on a tandem doing the school run with his younger son.