Aprire Cycles: manufacturing carbon frames in the UK
Brand says that there are major advantages in its UK-based model
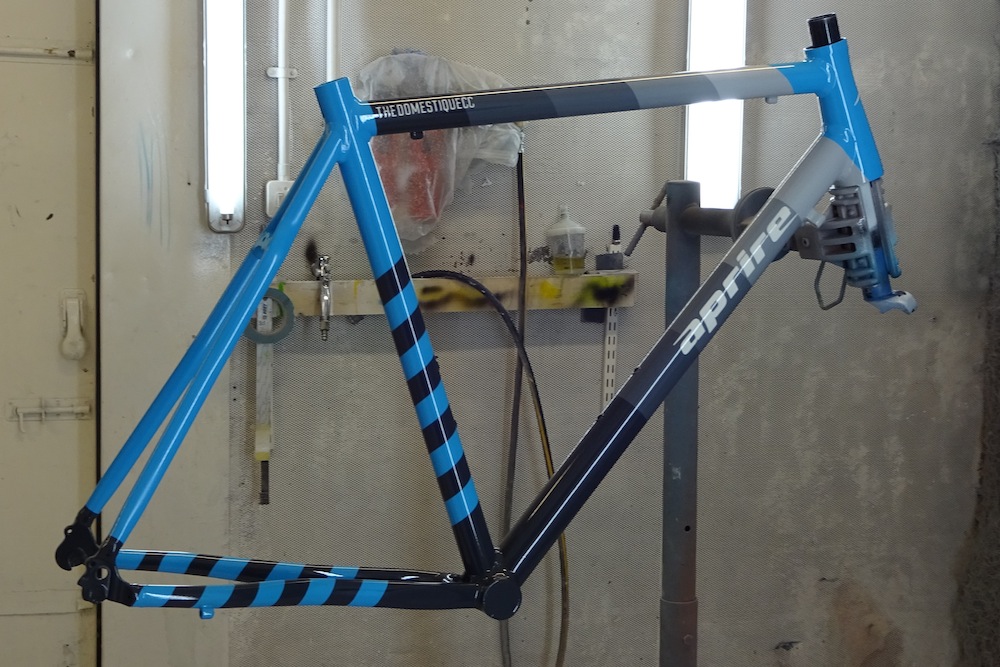
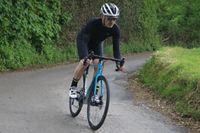
There’s a tendency to think that carbon frames have to be made in China. But Aprire Cycles is going against the flow and has set up its carbon manufacturing in Cheam, South London.
China has its downsides as a manufacturing base. Although labour costs are low, there’s high staff turnover: up to 20% each time there’s a national holiday.
And the cost of production of a set of steel moulds for frames in five sizes is over $50,000, while energy costs for the open heat presses used to cure frames are high.
>>> Cheap Chinese carbon imports: are they worth the risk?
Plus there are the third party manufacturer’s overheads and margins and the cost of shipping on top.
Aprire’s founder and chief engineer Phil Dempsey had over ten years’ experience working for big name brands in Taiwan and the US before returning to the UK.
>>> Price spikes and stock shortages possible after major shipping firm goes bust
The latest race content, interviews, features, reviews and expert buying guides, direct to your inbox!
He says that with more efficient mould production and curing processes his costs for UK production are only around 15% greater than in China.
Aprire uses tube-to-tube construction for its carbon frames, in which internal lugs join the frame’s main tubes together and the junctions are wrapped in further layers of carbon fibre.
Nevertheless, Dempsey says Aprire’s frames weigh around 850g for a painted size 54 in its top Vincenza model and 900g for the Celeste.
Dempsey says that with tube-to-tube construction it is easier to control how the carbon fibre plies sit relative to each other than with a monococque design.
Aprire uses a Finite Element Analysis software package to analyse how its frames respond to different stresses placed on them in use, modelling how much stress is placed on the frame and how it will respond to it.
Fine tuning the frame is a matter of judgement though: in some places, such as the seat tube, more flex in the frame is better as it leads to a more compliant ride.
The other key analysis technique is Computational Fluid Dynamics, to model airflow over the frame’s tubes. Aprire is using CFD extensively in designing a new aero frameset to be released in 2017.
It is also making small design changes to the Celeste for 2017.
As well as its carbon framed bikes, Aprire also sells the alloy Inverno road and Inverno AR all-road/cyclocross models.
They’re made in the Far East, but Dempsey has plans to bring alloy frame manufacture in-house too.
Watch: How are titanium bikes made?
Once the frameset has been made, Aprire paints it in house. It offers 15 standard colours, although most buyers elect to pay a bit more and choose from its range of over 8000 bespoke options.
>>> Inside a custom framebuilder's workshop
The painted frame is then built up to a customer’s specification selected from a range of full Shimano and SRAM builds, although you can buy frame-only too.
Aprire’s bikes are used by the Aprire-HSS Hire women’s race team and Aprire will be supplying bikes to a yet-to-be-announced men’s team too in 2017.
It offers a three day test ride option for potential buyers and ships its completed bikes out to selected dealers for a final inspection before collection by their new owners.
It’s an interesting manufacturing model and we’ll be looking to test one of Aprire’s UK made bikes in the next few months.
Thank you for reading 20 articles this month* Join now for unlimited access
Enjoy your first month for just £1 / $1 / €1
*Read 5 free articles per month without a subscription
Join now for unlimited access
Try first month for just £1 / $1 / €1
Paul started writing for Cycling Weekly in 2015, covering cycling tech, new bikes and product testing. Since then, he’s reviewed hundreds of bikes and thousands of other pieces of cycling equipment for the magazine and the Cycling Weekly website.
He’s been cycling for a lot longer than that though and his travels by bike have taken him all around Europe and to California. He’s been riding gravel since before gravel bikes existed too, riding a cyclocross bike through the Chilterns and along the South Downs.