CeramicSpeed Driven: wind tunnel data shows it's more aero too
New wind tunnel data shows the Driven drivetrain could save up to 8 seconds over 40km
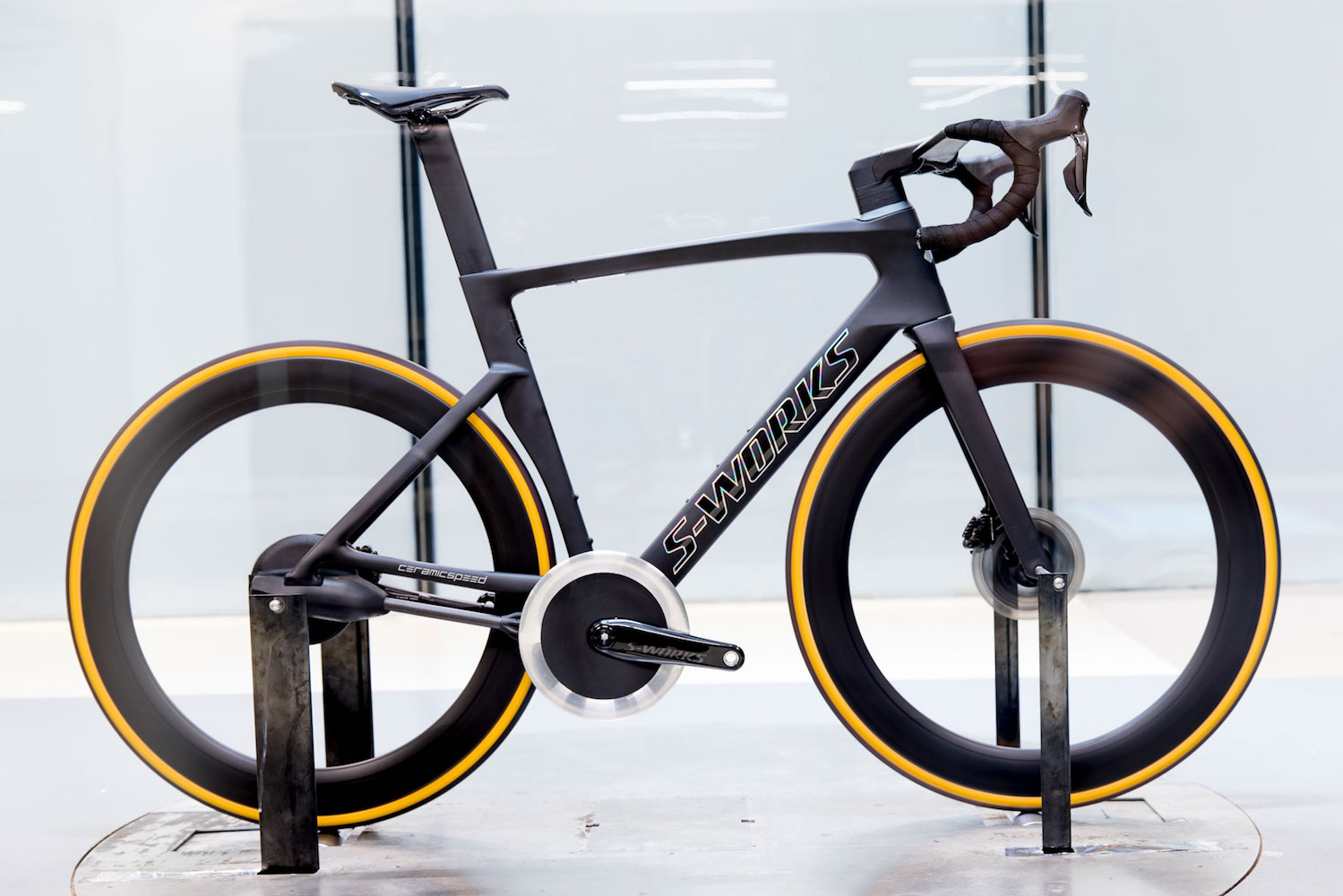
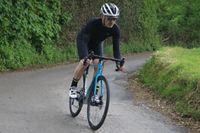
CeramicSpeed has taken a Specialized Venge aero bike, kitted out with its super-efficient Driven drivetrain to Spesh’s in-house Win Tunnel wind tunnel, to quantify its aerodynamics.
>>> What's it like inside a state of the art cycling wind tunnel?
With the rear wheel driven by a shaft rather than a chain, there’s a lot less gubbins hanging off the chainstay to disrupt the airflow around the rear wheel. CeramicSpeed says that Driven added 3% aero improvements over a conventional drivetrain on the Venge. That efficiency was found consistently over a range of wind yaw angles. Ingmar Jungnickel, Aerodynamics R&D Lead at Specialized, says that this could equate to up to 8 seconds time saved over 40km.
CeramicSpeed worked with the Mechanical Engineering Department at the University of Colorado to develop its Driven drivetrain system, which works with a carbon fibre drive shaft rather than a chain.
According to Jason Smith, CeramicSpeed’s Chief Technology Officer, who heads the Driven Project: “Advancements in drivetrain technology have been evolutionary since the 1920s. Driven is truly revolutionary given its unique rolling element power transfer and unmatched efficiency. The Driven concept has the ability to change the way the cycling industry views drivetrain design and drivetrain efficiency.”
CeramicSpeed claims that it’s the world’s most efficient drivetrain, with 49% less friction than the best derailleur-based systems and 99% efficiency. It says that there are 21 CeramicSpeed bearings used to reduce friction in the Driven system.
They are arranged around the edge of the driveshaft at its two ends and mesh with teeth on the chainring and the cassette which are oriented transversely rather than in line with the chainset and cassette. CeramicSpeed says that its bearings have very low rolling friction along with high durability. Moving the 13-speed rear cog across the cassette allows Driven to change gear ratios.
The latest race content, interviews, features, reviews and expert buying guides, direct to your inbox!
CeramicSpeed says that there are eight points of sliding friction in a conventional drivetrain, where the chain links move relative to each other. The Driven system bypasses all of these.
There’s still no word from CeramicSpeed on when Driven will come to market though.
Thank you for reading 20 articles this month* Join now for unlimited access
Enjoy your first month for just £1 / $1 / €1
*Read 5 free articles per month without a subscription
Join now for unlimited access
Try first month for just £1 / $1 / €1
Paul started writing for Cycling Weekly in 2015, covering cycling tech, new bikes and product testing. Since then, he’s reviewed hundreds of bikes and thousands of other pieces of cycling equipment for the magazine and the Cycling Weekly website.
He’s been cycling for a lot longer than that though and his travels by bike have taken him all around Europe and to California. He’s been riding gravel since before gravel bikes existed too, riding a cyclocross bike through the Chilterns and along the South Downs.