What's it really like inside a state-of-the-art cycling wind tunnel?
We take a look at the Flanders Bike Valley cycling wind tunnel
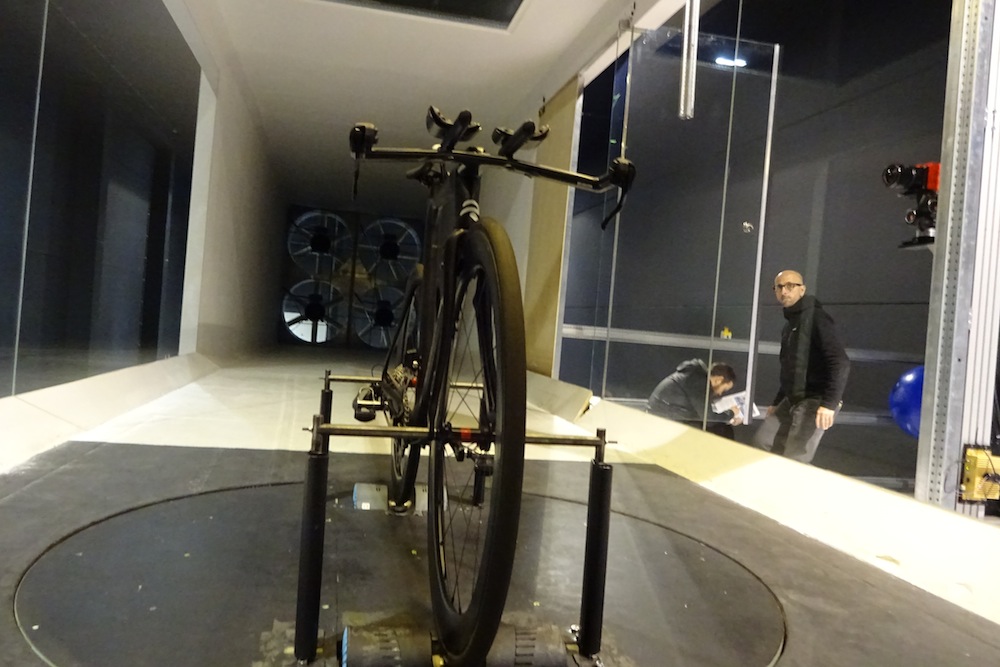
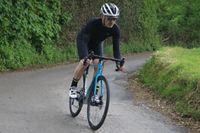
With aerodynamics the cutting edge of design for bikes, components and clothing, airflow modelling and wind tunnel testing of new products are key for the bike industry. But many wind tunnels are primarily designed to test aviation and motorsports products, where the velocity is much faster than for sporting goods.
So Belgian bike manufacturer Ridley, helmet maker Lazer and clothing manufacturer Bioracer collaborated to develop the Flanders Bike Valley windtunnel on a site next door to Ridley’s factory in East Belgium.
In general, says Bert Cellis, CEO of the Flanders Bike Valley, forces acting against a rider at 50kph on a flat road require around 500W power output to overcome. Of this, 5% is mechanical within the bike and 8% is rolling resistance from the road and tyres. That leaves between 85% and 90% – around 430 Watts – down to air resistance.
>>> How to be more aero on your road bike (video)
And a rider putting out 500W will generate around 2000W of heat, so keeping the rider cool is important too.
Wind tunnel design
The Flanders Bike Valley wind tunnel is 50 metres long with the entry port three times the area of the measuring cell, so that air speeds up as it flows through the cell. It has a 5cm deep honeycomb structure in the front vent, designed to ensure that air entering the tunnel is flowing smoothly.
Built out of metal struts, covered with boards, the tunnel is raised above the building’s floor. The interior of the wind tunnel is plastered, as this presents a smooth, airtight surface and helps reduce air turbulence, leading to more consistent results.
>>> Which aero bike is the fastest?
Air is sucked through the tunnel by four fans at its end. These generate a maximum of 270hp, for a maximum wind speed of 108kph. The air circulates back to the wind tunnel’s entry point through the surrounding building.
At the heart of the wind tunnel is a 6.5m long measuring cell. It’s designed to be long enough to test the effects of drafting. The measuring platform itself floats on air bearings which offer no resistance to drag. It can be turned to test at different yaw angles.
>>> Power v aerodynamics: how to get the balance right
The rider or bike to be tested sits on a turbo trainer and there’s a second roller under the front wheel that can be used to spin this at the same velocity as the rear wheel. Strain gauges under the platform measure the force generated by wind resistance, with accuracy to 0.1 Newtons.
>>> How much faster are aero wheels?
As well as presenting results in the control room, they are projected in front of the rider, so that they can immediately see the impact of position changes on drag and power output.
Airflow testing
Airflow testing has traditionally been done using smoke streams. But these cannot generate quantitative measurements. The Flanders wind tunnel uses oil droplet streams to measure airflow.
Droplets are introduced into the airstream, then a pulsed laser is used to illuminate them at 5 microsecond intervals as they pass over the object being tested. Synchronised to an ultra-fast camera, the movement vector of an individual droplet can be calculated, allowing quantification of airflow and identification of causes of turbulence.
The technology has been used in Formula 1, but this is the first time it’s been available for cycle testing. Because of the powerful laser used, it cannot be used on human subjects though.
>>> What effect do tyres have on aerodynamics?
Sitting on the floor in a corner of the control room was a dummy Tony Martin. It’s been used to test airflow over the rider and the effect of different fabrics on drag. Some fabrics present less drag than others – and the result is different dependent on the air speed and factors such as the curvature of a rider’s back. Even socks can make between 5W and 10W difference.
The wind tunnel’s maximum wind velocity is 108kph, a bit high for most bike testing. But the facility has also been used to test equipment in other sports such as skiing, bobsleigh and speed skating. And other cycling disciplines such as MTB racing and cyclocross are now taking an interest in aerodynamics too.
Alongside the wind tunnel, the Bike Valley building includes a business incubator. It houses over 30 cycling related businesses and has provided consulting services for clients including Sustrans as well as safety, healthcare and tourism businesses. World Tour teams using the wind tunnel have included Lotto Soudal, Katusha, BMC and Team Sky.
It’s also open for private testing, with options from a 30 minute position optimisation for 125 Euro up to a three day aero fit, wind tunnel session and track test at 6000 Euro.
Thank you for reading 20 articles this month* Join now for unlimited access
Enjoy your first month for just £1 / $1 / €1
*Read 5 free articles per month without a subscription
Join now for unlimited access
Try first month for just £1 / $1 / €1
The latest race content, interviews, features, reviews and expert buying guides, direct to your inbox!
Paul started writing for Cycling Weekly in 2015, covering cycling tech, new bikes and product testing. Since then, he’s reviewed hundreds of bikes and thousands of other pieces of cycling equipment for the magazine and the Cycling Weekly website.
He’s been cycling for a lot longer than that though and his travels by bike have taken him all around Europe and to California. He’s been riding gravel since before gravel bikes existed too, riding a cyclocross bike through the Chilterns and along the South Downs.