Are bicycle tyre tests lying to you? Rethinking rolling resistance and drum resting
Steel drum tests are currently the industry standard, but the more we understand about rolling resistance the more it becomes clear that they do not accurately reflect the dynamics of real road surfaces
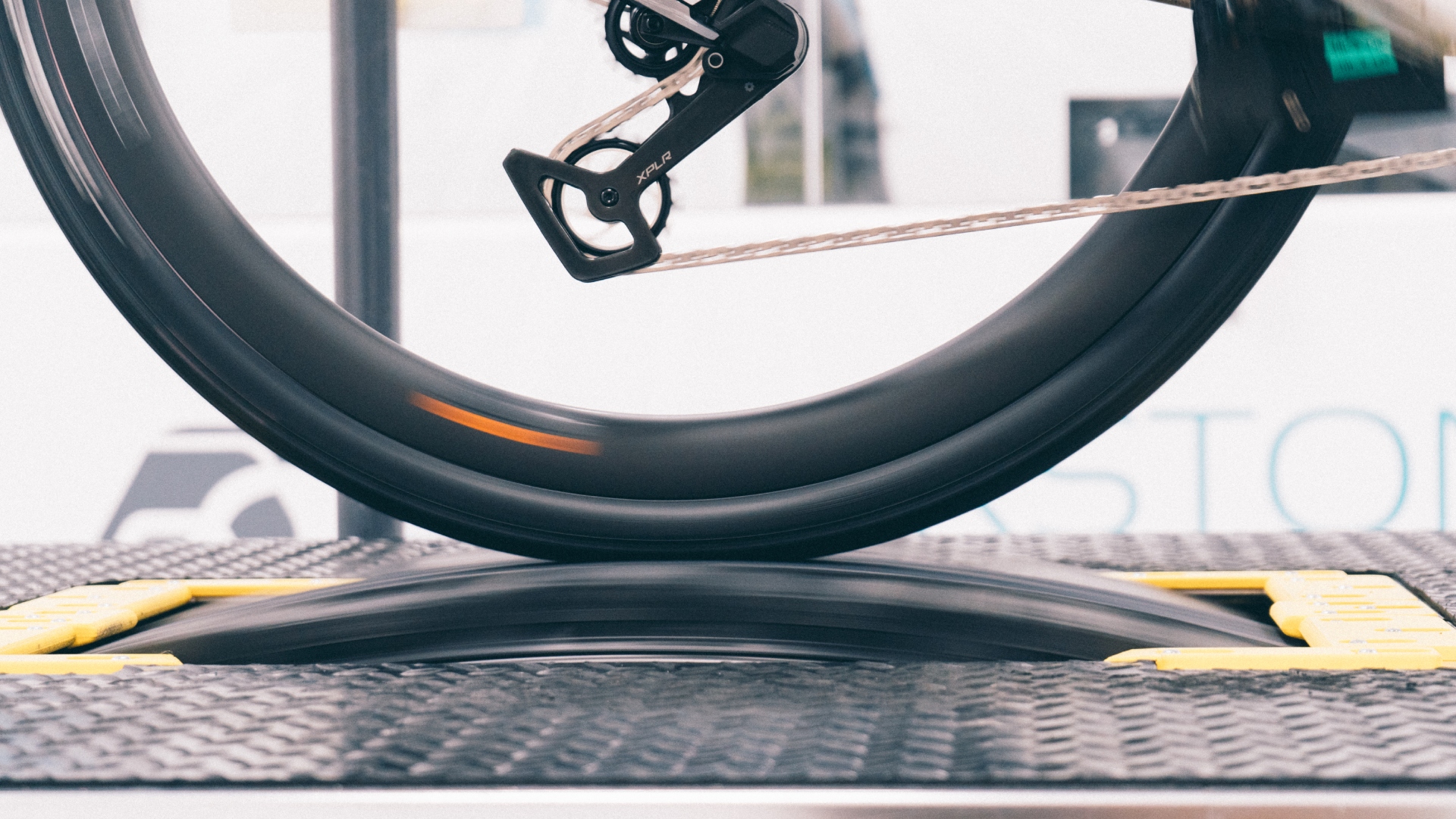
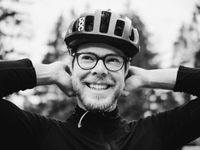
In the quest for developing the fastest tyre, rolling resistance is one of the most talked-about, and misunderstood, metrics in cycling. At the root of this obsession is a deceptively simple question: which tyre is fastest? More specifically, how much force is required to roll a tyre over a surface?
The answer lies in rolling resistance, or more precisely, the coefficient of rolling resistance (Crr), which is a complex measure influenced by tyre pressure, speed, road texture, rubber compound, rider weight and more.
Despite advances in technology, the cycling industry continues to measure rolling resistance the same way it has for decades now: the steel drum test. This approach involves spinning a wheel and tyre against a smooth steel cylinder while measuring the power required to keep it moving. It’s a controlled, repeatable way to quantify one key source of energy loss caused by the deformation of the tyre casing, known as hysteresis loss.
Tyre companies designing and testing products can use roller tests to compare tyres against one other without needing to take into account the plethora of environmental variables introduced by outdoor testing. And, on a completely smooth surface, like a velodrome, this testing correlates reasonably well.
But the world is not surfaced like a velodrome.
On actual, paved roads (not to mention unpaved) things get a lot more complex. A steel drum can measure hysteresis, but it does not reflect another major aspect of rolling resistance, called impedance or suspension losses. In the words of Silca’s Josh Poertner, these are “the losses due to the bouncing, jostling, and vibrational losses introduced into the rest of the bicycle/rider system by road vibrations.”
Poertner, who has worked extensively with World Tour teams to help them better understand how to optimise their equipment, explains these two considerations thusly: “If you plot Crr on a drum test, you will find that Crr decreases asymptotically as pressure increases. However, if you plot Crr in field testing, you see that there are two distinct regimes of Crr, the first one dominated by casing losses, and the second one dominated by impedance losses. Drum testing is only useful in predicting the regime dominated by casing losses.”
The latest race content, interviews, features, reviews and expert buying guides, direct to your inbox!
In other words: drum testing fails to capture this second category of losses entirely. It tells only part of the story.
That's not to say that drum testing isn't useful. According to Poertner, drum testing can certainly help in “predicting the relative differences between tyres. So the drum will be a poor predictor of actual Crr on any non-smooth surface, but if tyre A is 3% faster on the drum than tyre B, it will be very close to 3% faster on real world surfaces.“
But even here, in discerning how tyres perform relative to one another, there are limitations.
An additional issue with drum testing is that the size of the drum skews how different tyres perform. A small diameter drum measures more hysteresis loss on tyres at lower pressures or with more tread simply as a result of the drum shape, which digs into the tyre in a way that actual riding surfaces do not. Roads are quite flat, comparatively, and a roller drum would need to be enormous in order to accurately reflect this.
Since drum testing only shows one aspect of losses, higher pressures appear to have lower rolling resistance. And, for a long time, this was the prevailing belief in cycling. We now know this to be false. When it comes to actual, real life surfaces, lower pressures reduce impedance losses, which become more significant as surfaces get bumpier.
Alternatives to drum testing
Since real world testing has such a high number of factors to consider, such as weather variability, surface changes, rider fatigue, etc. getting accurate results is tough. All of these factors make this testing much more expensive and time consuming than drum testing.
Poertner's preferred testing method is called the Chung Method, also known as Virtual Elevation Testing.
"It's a great way to predict Crr in field testing, and has proven invaluable in optimising setups for both equipment choice, as well as finding optimal tyre pressure for a given surface," says Poertner. "This method has the benefit of being useful on the actual surfaces you want to test.”
The basic premise of the Chung Method is to ride a short, stop-free course several times at a variety of power outputs (a power meter is necessary, as is a way to accurately measure speed and altitude gain). It is also critical to test on a day without wind. By repeating this test with different tyres, one can isolate the true coefficient of rolling resistance of each tyre on the surface at hand.
This style of testing also can be useful for making aerodynamic improvements to one’s setup, but the tough part is that it is often very rider and conditions specific. Like aerodynamic optimisation, what works for one person may or may not work for others. Also, gravel races do not have consistent surfaces—some of the race might be paved while other parts might be extremely rugged. Riders have to decide which part of the course to prioritise their equipment for, making educated guesses as to what tyre and tyre pressure will provide the best option for their hoped-for racing or riding outcomes.
Another testing technique is the roll down test, whereby a rider repeatedly rides down a hill with tightly controlled variables in an attempt to isolate the tyre’s losses. This testing methodology is simple, but requires very specific conditions in order to find effective results. The benefit is that it removes some of the additional variables present in the Chung method.
An ideal scenario, with the ultimate control over testing variables, would be to bring an outdoor surface indoors. This is theoretically feasible, but would take immense resources in order to be realised. Something similar is being done in the Catesby Tunnel in the Northamptonshire countryside in England for testing aerodynamics (more about that here). Maybe if we all write the Catesby Tunnel Test Facility a letter they’d be willing to surface one half of the road with gravel from Emporia, Kansas? I’ll be the first one in line if it happens!
Conclusion
Figuring out a tyre’s true rolling resistance is anything but simple.
While roller drum tests offer a convenient way to compare tyres in controlled settings, they only tell part of the story. Real-world methods like the Chung Method or roll-down testing can get us closer to the truth, even if they come with their own challenges. There’s no perfect solution just yet. But as our understanding (and our roads) evolve, so too will the ways we measure what really makes a tyre fast.
Thank you for reading 20 articles this month* Join now for unlimited access
Enjoy your first month for just £1 / $1 / €1
*Read 5 free articles per month without a subscription
Join now for unlimited access
Try first month for just £1 / $1 / €1
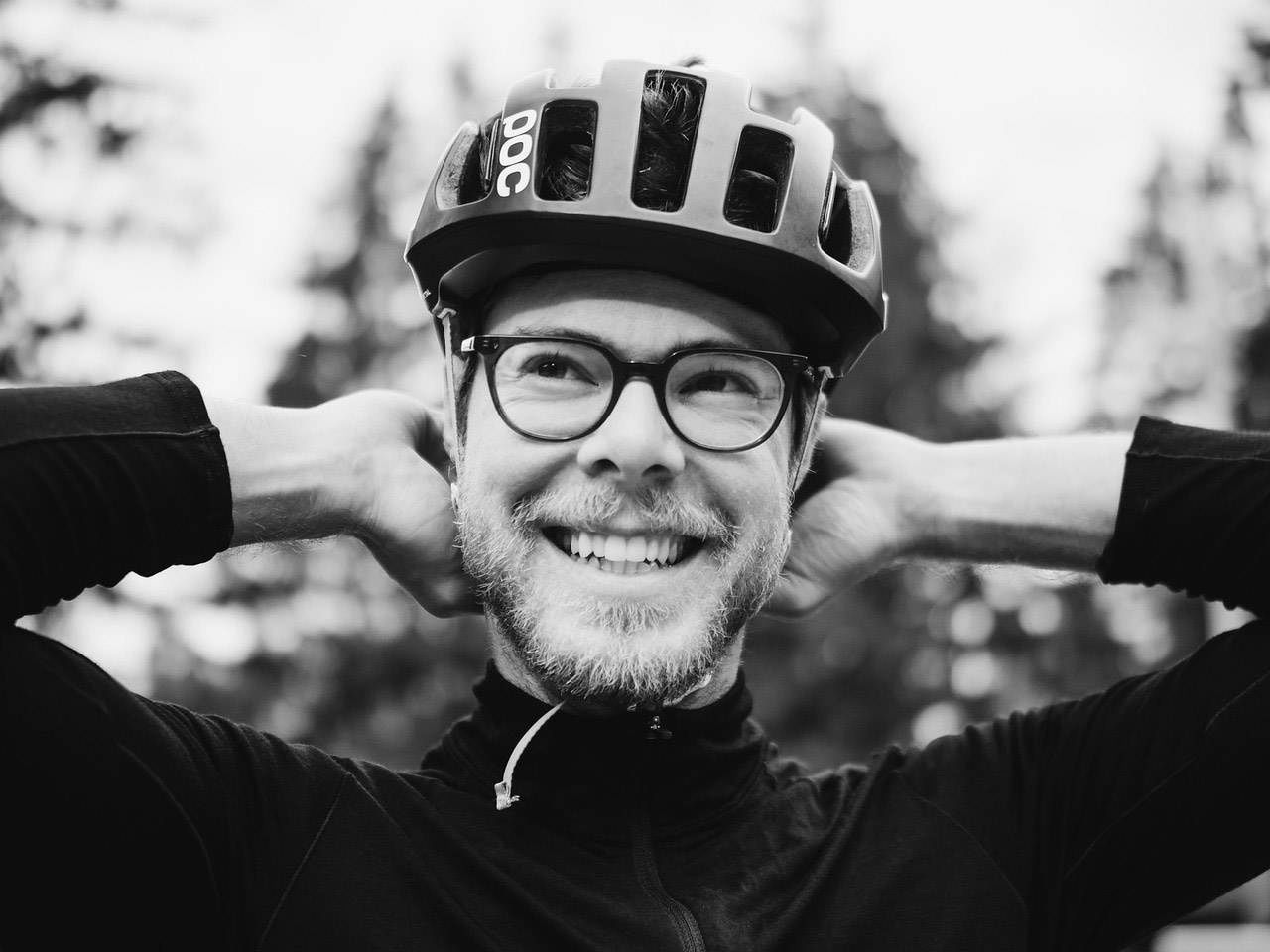
Tyler Boucher is a former (and occasionally still) bike racer across several disciplines. These days, he spends most of his time in the saddle piloting his children around in a cargo bike. His writing has appeared in magazines published in Europe, the UK and North America. He lives in Seattle, Washington.
You must confirm your public display name before commenting
Please logout and then login again, you will then be prompted to enter your display name.