How Gaerne makes its cycling shoes
It takes 109 pieces to make Gaerne’s top-end G.Stilo+ cycling shoe. Here’s how its shoes are assembled.
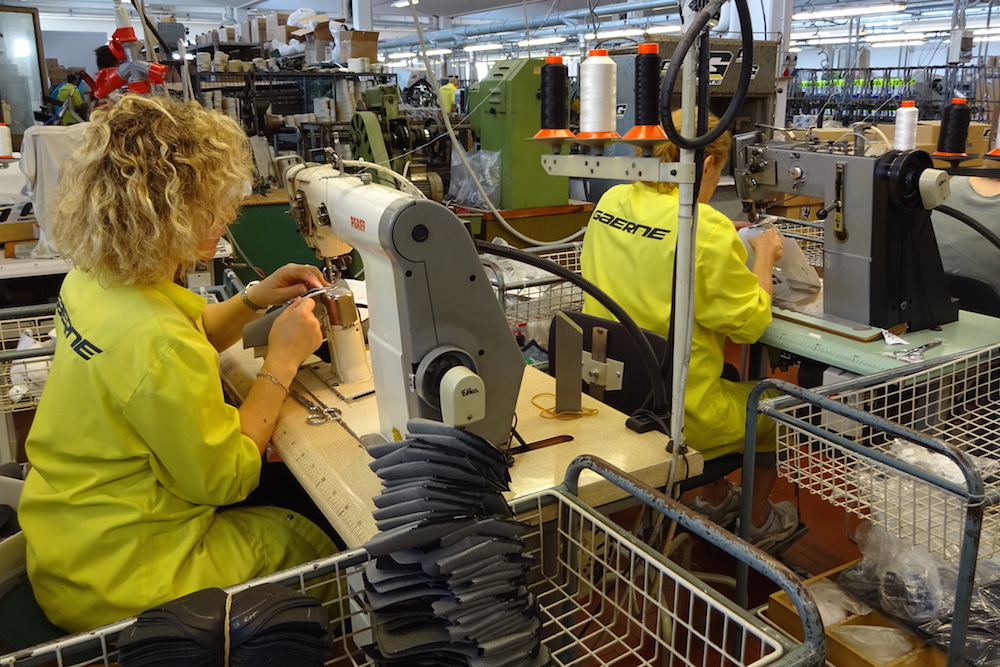
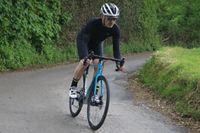
Based near Asolo in northern Italy, Gaerne prides itself in its all-Italian production and quality. Founded in 1962, the company still makes mountain footwear, its original product. But it’s been making cycling shoes since the 1980s and also makes a wide range of motorcycle boots.
It’s a family business, with founder Ernesto Gazzola in his 80s still in the factory every day and his children Gianna, Gianni and Marta running different parts of the business. Its 55 employees produce 79,000 pairs of cycling shoes and 116,000 pairs of motorcycle boots every year.
The company says it takes up to two years to design a new shoe and bring it to market. During that time, it works closely with companies such as Boa to ensure that its closures are used optimally. It worked with Speedplay on its four-bolt sole for its G.Stilo+, which is the only one approved by Speedplay.
Gaerne buys the microfibre for its shoes’ uppers in bulk, then cuts the rolls up into blanks that are laser cut and perforated off site. Gaerne sews the component pieces together to assemble the shoe uppers and add the closures – in this case for a tri shoe.
>>> Best cycling shoes 2017: a complete buyer's guide
The next step is to glue the upper to the inner side of the sole. This is a two-part process that uses two different machines: first the toe box is assembled around the last, then the sides are stretched and glued into place. The glue is heated to 250C to ensure an effective bond.
The glued edges of the fabric are then sanded down to make them flatter before the carbon outer sole is glued in place and pressure is applied to bond the two pieces.
Finally the last is removed, the insole fitted and the shoes boxed for shipment. There’s a large warehouse of shoes awaiting shipment to shops and distributors, with bulk sea freight usually used to the USA and Australia.
Gaerne has racks of lasts for different foot sizes. There are also different male and female lasts and wider ones for Asian feet. Since the last is left in the shoe for up to a day after it’s been made, there’s a need for a lot of them.
There are lasts for some famous names, with most having some fine tuning to fit the wearer as well as custom insoles. Beside André Greipel, there are lasts for Fabian Cancellara, Alexander Kristoff and, poignantly, for Michele Scarponi.
There’s a long list of other famous pros who have raced in Gaerne shoes in the past too.
Thank you for reading 20 articles this month* Join now for unlimited access
Enjoy your first month for just £1 / $1 / €1
*Read 5 free articles per month without a subscription
Join now for unlimited access
Try first month for just £1 / $1 / €1
The latest race content, interviews, features, reviews and expert buying guides, direct to your inbox!
Paul started writing for Cycling Weekly in 2015, covering cycling tech, new bikes and product testing. Since then, he’s reviewed hundreds of bikes and thousands of other pieces of cycling equipment for the magazine and the Cycling Weekly website.
He’s been cycling for a lot longer than that though and his travels by bike have taken him all around Europe and to California. He’s been riding gravel since before gravel bikes existed too, riding a cyclocross bike through the Chilterns and along the South Downs.