Will cycling's wheel and tyre brands ever learn to play nicely?
The days of sacrificing thumb skin at the altar of fitment are numbered
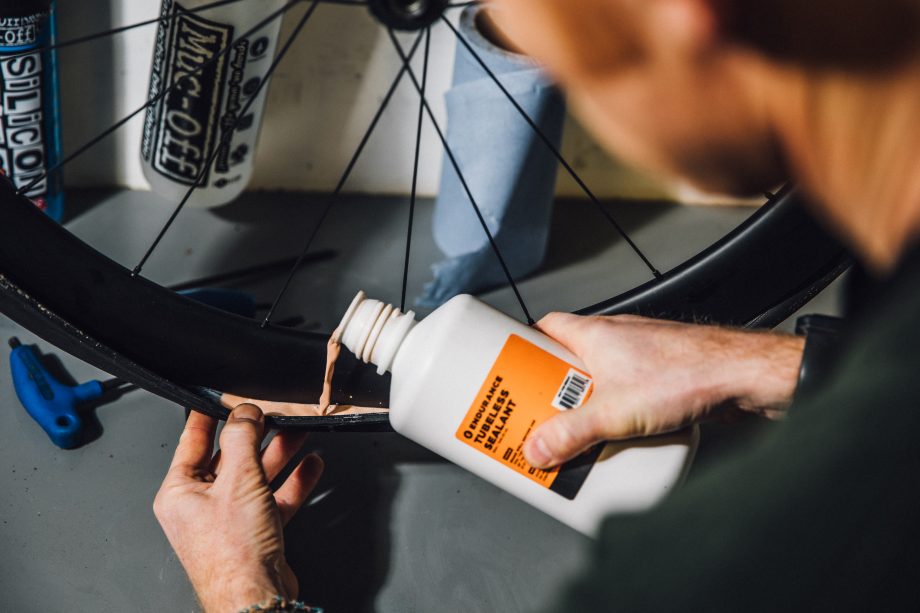
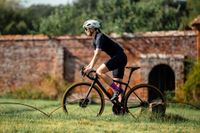
Imagine if you bought a new iPhone, and a matching, compatible case, only to find that the latter required an unreasonable number of phone case levers, some “technical soapy water”, a liberal dose of swearing and a sacrificial donation of the skin on both of your thumbs before the two would mate? It would be reasonable to suggest that either the phone, or the case, had failed to adhere to specified manufacturing standards. And yet, certain quarters of the cycling industry remain resolute in allowing this degree of incompatibility across wheels and tyres.
The matching together of bicycle tyres and bicycle rims is something of a russian roulette, governed by either-side deviations from absolute measurements, batch variance, and - in some cases - the introduction of proprietary technology. The advent of tubeless road tyres has made the situation a whole lot worse by introducing a need to seal as well as a need to fit, but, it may also herald a need for improvement.
“There’s an ultimate dichotomy between ‘do you make the tyre easy to fit, or do you make it easy to inflate?’” muses Schwalbe’s head of UK communications, Tim Ward. “You can’t get a tyre on without a certain amount of slack in the middle, but if you introduce too much slack, you won’t have a tight enough seal to inflate.”
Both wheel and tyre brands bare the brunt of the criticism when the two parts fail to meet in the middle, though, both passionately claim that they (sometimes unjustly) receive the bulk of the complaints.
Who governs all of this?
Jargon Buster
Just in case you're new here...
Clincher: Tyre that uses inner tubes
Tubular/Tub: Tyre that is glued on to the rim
Tubeless: Tyre that uses sealant, and no inner tube
Hookless: Wheel rim with no bead hooks, safety relies on the rim/tyre interface
For the uninitiated, it's important to know that bicycle wheels and tyres do not share a completely anarchic relationship. There are rule setters.
The standards for which width tyres are to be considered compatible with which width rims, and what pressure they can be run at, are set by the European Tire and Rim Technical Organization (ETRTO) and International Standards Organization (ISO).
Granted, progress can be slow. “When I was working for Campagnolo I was on the ETRTO committee,” remembers Hunt’s lead engineer Luisa Grappone (MSc Aerospace Engineering). “[At the time] they were discussing tyre width and rim width combinations, and it took seven years to come to an agreement.”
The latest race content, interviews, features, reviews and expert buying guides, direct to your inbox!
Recommended combinations of tyre widths, internal rim widths, and max pressures, are listed in a giant table by both bodies. Purchasing these resources in their entirety will set you back hundreds, and you'd be paying just as much for the advice on tractor tyres as road racing tyres. You can get the gist from the likes of Schwalbe's recommendations.
“I don't know whether making the ETRTO guidelines available online would make it any easier for consumers because it’s going to be a lot of dry, technical information," Ward says. "The average consumer probably wouldn't find it very easy to relate to the products available to them. As far as the public sector goes, as long as they understand that one or other is compatible or not, that’s as much as they need to know really.”
The ETRTO and ISO set the rules, “they don't really do the testing themselves,” Grappone points out. And, just because a pairing is deemed to be 'safe' via its claimed standard, it doesn't mean it's 'ideal'.
Can we all just tolerate each other?
Stock photo for illustration purposes only
Compatibility between tubless tyres and rims has absolutely improved since the technology first arrived on the road. Some models can even be inflated with a handpump, and personally, it's been a long time since I found myself exasperated by a seemingly repelling set-up. However, at Cycling Weekly, we still hear stories from readers who have been unlucky enough to purchase a dud pairing, and both Schwalbe and Hunt have been on the receiving end, too.
A tyre and wheel combination may sit well within ETRTO/ISO guidelines but still behave like arch enemies.
Explaining the tolerance (window of acceptable fit) allowed for each, Grappone vents, “the problem is that rims have very tight tolerances, we are talking about +/-0.5mm. Tyres go +/-6mm, though probably more +/-1mm for a narrower width. Tyre manufacturers deal with a different material.
“If my rim has a tolerance of +/-0.5mm and my tyre has a tolerance of +/-1 or 1.5mm, you can understand how difficult it can be combining those two components. You can be in the condition of the tyre being at the upper level and the rim at the lower level, and then it could be completely loose, or it could be the opposite, and you have a tyre that is really hard to fit on a rim.”
The situation is even further complicated by the emergence of the hookless standard among road rims. Hookless rims do away with the hook, which means that the tyre must fit the rim, and must not be overinflated, the risk factor being a rather ride ending spontaneous detachment between the two. This technology introduces a greater focus on standardisation for the sake of safety.
What happened when we intentionally overinflated a hookless tyre...
“We’re quite a long way away, in terms of bicycles, of getting to the point of motorcycles and cars in terms of tyre fitment standardisation,” Ward confirms what we all know, before explaining the why. “There’s probably more variation in manufacturing of bicycle tyres, they’re thin, floppy little things compared to a car tyre. [Also] I would say it’s probably down to the fact that, in most parts of the world, automotive products are fairly heavily regulated from a safety point of view.” The automotive industry is also far richer, and, cars are more expensive - no one wants an entry-level road bike to cost more than a brand new SUV.
“On a car, there’s 1000s of items - crash testing, emissions, lighting, the brightness of lights, colour of lighting, glass in the car, seatbelts, airbags, it’s endless…. Because it is so complicated, it costs millions - if not billions - to develop a new car. With large scale manufacturing like that, the more they can get standardised across their global markets, the easier it will be for them. If you have to do a different set of tail lights for every country, you can see how very quickly it gets very expensive,” therefore, it’s in the interest of car manufacturers to play nicely with tyre manufacturers.
In bicycle land, not everyone wants to play ball.
“Some brands, like ourselves, are really keen to push the agenda of a common platform for everybody to move forward on. Then, there are certain brands, going down the proprietary route, who are pushing back against that. Which is blocking those attempts to some extent,” Ward says, highlighting that obviously, if you make both rims and tyres, it’s beneficial to encourage customers to meet all of their needs via your own wheelhouse.
Where do deviations come from?
If the greatest issues in compatibility come from varying degrees of deviation form tolerance, the next sensible question is: why the deviation?
Both Grappone and Ward say that their processes are relatively controllable.
“On the rim side, it’s probably a lot easier than tyres,” Grappone suggests. “We make rims with steel moulds, we can control the thermal expansion of a mould to our oven, we can design taking into account the thermal expansion of the steel mould in the oven. So when we do dimensions, we take into account everything, and we can be sure to be within those tolerances. I guess, for tyre manufacturers, life can be a bit more difficult.”
Ward’s sentiment doesn’t quite align. “Variations in tyre manufacturing are fairly minimal. You get slight variations in the thickness of the tread layer, because it’s extruded [pressed out] under very high pressure - if you get any slight variations in that pressure you’ll get slight variations in the extrusion but we’re talking a tenth of a mm to 0.5mm. That will affect weight. We tend to have a weight of +/-8% as an acceptable tolerance.
“Weight is where you’ll get the most variation. That doesn't have much of an impact on inflation. The bead seat diameter is the critical part [in terms of fitment]. And we work that to a tighter, closer tolerance than we do for normal tube-type tyres, in the order of <1mm. That’s critical and stringently batch tested and assessed, and adds to the cost of manufacturing.”
There are other factors which can introduce difficulty. Referring to one brand producing proprietary rims and tyres, Ward reminisces over some particularly thick rim tape which worked only with the narrow cross-section bead of the accompanying tyres. “You only need to reduce the inner diameter by even 0.5mm, that multiples up over the circumference, to create quite a big difference,” he states.
Internal testing
Both Schwalbe and Hunt test their equipment with a range of potentially compatible mates. Last updated in December 2021, Schwalbe’s publicly available documentation details the results from internal testing of wheels from the likes of Campagnolo, Zipp, Enve, Shimano and more. Only one wheel was deemed “unsafe” with Schwalbe tyres, though several were “very difficult” to fit or inflate.
Hunt, equally, tests its rims with the tyres of popular manufacturers in house. However, quite understandably, neither can afford to carry out testing of multiple units, assuring consistency.
The industry guideline is that a hookless tyre/rim must hold 110% of the maximum pressure before hitting blow out - but most manufacturers aim for more, Schwalbe told us they go to 160%.
“We can't test all tyres. It is time-consuming, money consuming, and really not up to us,” Grappone frankly points out. “Once we do a tyre blow off test, that rim is thrown away, we wouldn't even keep it for internal tests.”
The agreement comes from Ward, “our tests are based on one pair of wheels. We’re not in a position to do massive batch testing, that would be very expensive.”
The way forward
Compatibility between carbon (or metal) and rubber has come to the fore with the growing trend towards tubeless tyres, and even more so with the increasing attention on hookless constructions.
Hunt, for example, was hesitant to follow the march towards hookless, holding back much longer than other brands - such as Zipp and Enve, who used the manufacturing technique to lower their prices with options such as the 303S and Foundation line.
The reason, according to Grappone, was a lack of belief in available tyres - something that, now addressed by larger brands such as Continental with its new GP5000 S TR, has ceased to be a barrier.
"The reason for us not going hookless [earlier] was mainly relating to the tyre options. Because Continental was not hookless compatible, there were fewer options. So, we decided to make most of our rims as hooked versions, to be sure that we were giving the right choice to our customers.
"From the moment that more and more tyre brands come to the market with safe tyres, we started to say ‘why not go to hookless?" she says.
Arguably, it's pressure from wheel brands - who want to pursue hookless systems - forcing tyre brands to work hard.
“For years and years, it was either tubular tyres, glued on, or tyres with tubes - we conformed to a general standard, but it didn't need to be as precise as with a tubeless tyre,” Ward notes.
And, thankfully, he believes that this increasing adoption will drive greater friendship between the two, or at least incentivise efforts.
“As much as the safety side, the competition side should help to drive compatibility, and force tyre and rim manufacturers to get their heads together. Look at the recent Flanders and Paris Roubaix, there are probably more riders on tubeless tyres than ever, and it’s increasing every year. That’ll drive the development of compatible products because you’ve got a mix of different tyre and wheel sponsors.”
In the meantime, what can consumers do?
“Consumers have to not assume. Understand the products. Ask the right questions of the right people. And research,” Ward advises. “If you’re using tubeless tyres, make sure the rim is clearly stated as tubeless compatible. If it's a hookless rim, check if the manufacturer lists any particular tyres as compatible. That doesn't necessarily preclude tyres that they don't list, it just means the ones they've tested. And always adhere to whatever the max pressure of the rim.”
That, and, a dose of “technical soapy water” - Ward’s name for Schwalbe’s ‘Easy Fit’ solution. You can rest assured, it is actually quite a bit more technical than a squirt of Fairy liquid, and hopefully, one day it'll become redundant.
Thank you for reading 20 articles this month* Join now for unlimited access
Enjoy your first month for just £1 / $1 / €1
*Read 5 free articles per month without a subscription
Join now for unlimited access
Try first month for just £1 / $1 / €1
Michelle Arthurs-Brennan the Editor of Cycling Weekly website. An NCTJ qualified traditional journalist by trade, Michelle began her career working for local newspapers. She's worked within the cycling industry since 2012, and joined the Cycling Weekly team in 2017, having previously been Editor at Total Women's Cycling. Prior to welcoming her first daughter in 2022, Michelle raced on the road, track, and in time trials, and still rides as much as she can - albeit a fair proportion indoors, for now.
Michelle is on maternity leave from April 2025 until spring 2026.