Your next road bike needn't be carbon: could steel, titanium or aluminum be a better choice?
Carbon is often seen as the default option - but a metal bike brings with it a lot of benefits
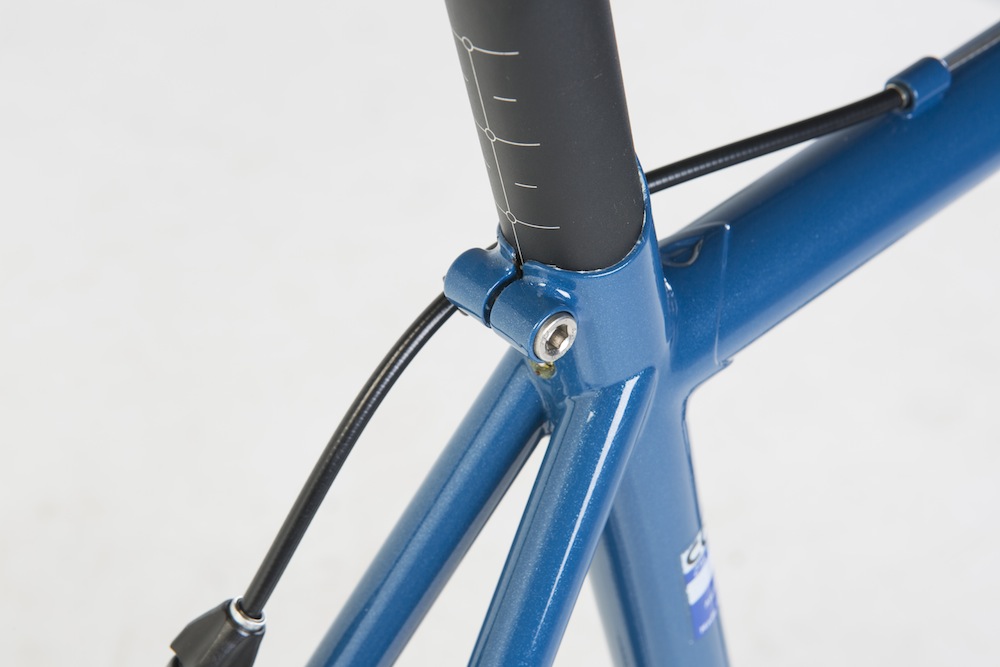
There are many decisions to make when buying a new road bike. Perhaps the most important of those is which frame material to choose. After all, the frameset is the heart of your bike, helping to define the overall ‘ride quality’ more than any other component.
When it comes to frame material there are four very distinct options: carbon, aluminium, steel and titanium. For many of us when we’re thinking about a modern road bike the discussion starts and ends with carbon. This is perhaps unsurprising. After all, it’s the material of choice for the professional peloton, the natural influencers for many roadies. There’s also bags of choice; carbon road bike frames are usually front and centre of all the major brand’s road bike line-ups. And of course it’s the lightest of all the frame materials, a selling point that still carries plenty of weight for most road enthusiasts out there.
So why look outside of carbon?
Carbon is light and stiff - but does that mean it's better?
Carbon frames are laid into a mould
Drop bar road bikes have their roots in professional cycling. This racing pedigree continues to permeate road bikes today, its influence pronounced, even if a large number of the bikes sold never actually get ridden competitively.
Race bikes are built with aerodynamics, stiffness and low weight at front of mind, so carbon is the obvious choice. Carbon frames are constructed in a mould, the material is malleable, and more easily shaped at the dictation of windtunnel results. It also carries a stiffness-to-weight ratio suited to pro riders.
Many of the carbon road bikes we’re being sold today are initially created with the best bike racers in mind - that applies even to endurance bikes, like the Specialized Roubaix and Trek Domane - both have made appearances at Paris-Roubaix, for example.
With brands spending huge sums of money on research and development designed to help professional riders save a few milliseconds here and there, it figures that they’ll need to claw some of this investment back by encouraging us to covet these same bikes. Even if they aren’t perhaps what we always really need.
“There was a push in the bike industry to make things bigger and stiffer,” says Fergus Liam, US Marketing Manager for Ritchey, a brand synonymous with steel but who also makes frames using carbon. “The result was bikes that all acted the same.”
“We were informed by the high demands of bike racing that said stiffer is better,” he tells Cycling Weekly. “However, this is akin to having an F1 car inform how a sedan [a saloon in the UK] should operate - the day-to-day ride quality will be terrible at best.”
If you're beginning to wonder if you might be better off on the bike equivalent of a sedan, read on...
Steel as a road bike frame material
Steel at a glance
Pros: Comfortable yet lively ride quality, durable with custom builds an option
Cons: Likely heavier than its counterparts
Who's it best for? Randonneurs, tourers and those who value added compliance in their road bikes
While steel may appear to be forever making comebacks, the truth is it never really went away.
“Steel has a liveliness that is exhibited rarely in other materials,” says Liam. “It is forgiving and repairable yet precise in how it prefers to be constructed.”
Balancing utilitarian practicality with discernible performance characteristics means steel can still meet the demands of today’s road bike users. Little wonder then that it is adopted with enthusiasm by framebuilders one generation after another; the passing of a torch that serves also to shine new light on the oldest of materials.
Tom Ritchey began making steel bike frames as a 16-year-old in his Northern Californian home. In 2022 he marked the 50th anniversary of his first welded frame, a birthday that served as a reminder of steel’s continued relevance. “Tom perfected his lugless method of construction through his brazing and developed Logic tubing as a result,” Liam says “The tubing was designed to produce the best ride quality the material could yield while remaining durable without sacrificing weight.”
Steel tubing can be single gauge or butted. Butted tubes have a constant diameter on the outside but variable wall thickness. This allows the builder to add strength in places while reducing weight in others. A double-butted tube for example is thicker at each end. A triple-butted tube has three different wall thicknesses.
There’s also progressively butted tubes, such as those made by Columbus. British brand Mason Cycles uses this tubing on its all-road Resolution frameset. “There are no steps between each wall section which could lead to stress-raisers and weakness,” says founder Dom Mason. The Columbus tubing can be drawn to very thin wall dimensions, just 0.4mm in the centre section. It’s the reason that many of the lightest performance steel frames are made using Columbus’ Life and Spirit tubing.
Ritchey uses its proprietary Logic tubing in all its steel bikes. As a brand that has a road frame, a cross frame, a gravel frame and an ‘adventure’ frame all made from steel in its current line-up, it’s strong evidence of the versatility of the material.
“Logic tubing uses force and direction specific butting profiles that are unique to the location and size of a frame so as to maintain strength while reducing weight as much as possible,” says Liam. “The butting of the top tube at the head tube isn’t the same profile as the top tube at the seat tube, and that profile isn’t the same on a small as it is large.”
Steel in the pro peloton
For the best part of a century steel was the only choice for road bikes, and therefore, bike racers. Maurice Garin rode a steel La Française Diamant that weighed 18 kilograms on his way to winning the first Tour de France in 1903. The last rider to win the Grande Boucle on a steel frame was Miguel Indurain in 1994, this time aboard a nine-kilogram Pinarello that may actually have been a Dario Pegoretti creation in disguise.
In between many more legend’s names were etched in stone but created with the help of steel. Coppi and Bartali, Anquetil, Merckx and Hinault all won the great race, and dominated their sport, aboard steel framed bicycles. As both production methods and frame design evolved the newer steel tubing became an ideal match for the demands of the sport. It was light yet strong and stiff. It was also affordable and easy to shape and machine.
Modern steel road frames feature tubing that’s often oversize when compared to steel frames of yesteryear to allow for the use of the aforementioned thin wall sections without losing strength. Builders will also use custom shapes and bends to help them to attain the ride quality they are seeking.
“We don’t use ‘off the shelf’ tube sets,” says Mason. “We take time to choose each tube individually, considering the influence that it will have on ride quality and overall performance. We will use a blend of tubing types to help us achieve this goal.”
Even taking into account the change in modern steel tubing, it’s a far cry from some of its carbon, titanium and aluminium counterparts. This is particularly noticeable around the bottom bracket and the headtube where the search for improved stiffness has led to beefed up profiles that dwarf steel equivalents. But for Ritchey, when it comes to steel, size certainly isn’t everything.
“We stick to using a straight steerer for a variety of reasons but mainly it’s a matter of strength and not over engineering when it’s not needed,“ Liam says. “Steel functions best in smaller diameters that help reduce weight while remaining strong and responsive.”
Strong and light is a desirable combination for any bike frame. It’s one that all materials seek to provide, whether it's steel, aluminium, titanium or carbon. Interestingly steel, aluminium and titanium all share the same strength-to-weight ratio. But as steel is the denser of the three, attempting to match the frame weight of a titanium or aluminium bike would lead to tube walls that were too thin to be durable. Hence the reason that Ritchey, and others, keeps the tube diameter of its steel bikes smaller at the expense of a little added weight.
Reynolds and Columbus tubing
While there are a number of brands associated with steel tubing, Reynolds and Columbus are true titans.
The British and Italian manufacturers are synonymous with the material; both have been at the heart of many Grand Tour winning machines, including Fausto Coppi’s legendary Columbus-tubed Bianchi Folgore that he rode to success at the 1947 Giro d’Italia and Eddy Merckx’s private-label DeRosa that was built with Reynolds 531 and helped him win the 1969 TdF.
The latter was born in 1935 and named because of the 5-3-1 ratio of manganese-steel alloy used to make it. But Reynolds tubing dates back to 1898, with the Birmingham-based outfit the inventors of butted tubing. It’s still going strong today, with its 853 tubing a popular choice for frame builders wanting premium quality, lightweight steel tubing.
Columbus has a similarly rich history. It began in 1919 on the outskirts of Milan, started by Angelo Luigi Colombo, with makers of seaplanes, automobiles, motorbikes and furniture among his first clients. However it became a favourite of many bicycle frame builders from the 1930s onwards.
In the late 1970s, a new ‘Columbus’ company was formed by Angel’s son. While the brand has expanded, tubing is still central to its business, with its seamless XCr tube sets highly coveted for their low weight without sacrificing strength or durability.
As for this weight, the most often quoted reason for cyclists not choosing a steel road bike, Liam thinks we need to reevaluate our thinking.
“First off, I think we need to get off this weight issue,” says Liam. “A bike that rides well isn’t solely determined by weight. That isn’t to say a well crafted steel bike can’t be light and ride well. We have a Ritchey Road Logic here with alloy parts and tubed wheels that tips the scales at 18lbs (8.16kg). That’s no slouch."
But he, along with every other frame builder we spoke to, believes that steel’s performance characteristics live outside of a world where we obsess over each and every gram that makes up our road bikes overall weight.
“A well-produced steel bike will outperform its carbon or aluminum counterparts in ride quality and resilience any day of the week,” Liam says.
“Steel has a unique property in that it can flex and bend and give when needed,” he continues. “The analogy I most often use is it’s not what you notice on the ride but what you don’t notice. Excess fatigue or soreness that might be associated with riding a bike is dissipated. Equally a good steel bike will feel grounded in a way that is confidence inspiring.”
The comfort that Liam finds in riding steel bikes is one shared by many. It’s perhaps the material’s greatest asset. If you’re after a road bike for long days in the saddle, with the ability to adapt to a variety of road surfaces, a well-designed, high quality steel frame is likely to deliver a more comfortable ride than any of the other competing materials. We've been particularly impressed with the Fairlight Strael 3.0, to give just one example.
Aluminium as a road bike material
CW's Sam Gupta was obviously impressed with the new Specialized Allez Sprint
Aluminium at a glance
Pros: Often cheaper than other materials, can offer similar ride to a carbon frame
Cons: While it can deliver ride attributes of carbon, it’s unlikely to be quite as light or as stiff
Who's it best for? Racers on a budget
After steel’s regin in the professional ranks came to an end, but before carbon became the material of choice, aluminium had its moment in the sun.
It offered many of the attributes that would make carbon so popular, in that it's both light and stiff, but was considerably cheaper to produce. While it didn’t stay at the top of professional cycling for long, it has remained relevant as a frame material, with its lower cost compared to carbon, steel and titanium an obvious bonus.
“Aluminium has the advantage of being relatively economical to produce and easier to manipulate and form than other materials like steel and titanium,” says Mason. “This means that the finished product, although still high performance, does not have to be high price.”
Indeed the best aluminium road bikes are usually chosen for their ability to balance ride quality with price tag. While on the whole, it’s probably not as light and stiff as carbon, aluminium technology has progressed in recent years and good aluminium often beats cheap carbon. Dom Mason concurs. “In my opinion it makes way more sense to own a highly developed Alu frame, rather than a cloned composite frame of the same price,” he says.
“By using clever tube manipulation, advanced tubing and sensible design, a modern aluminium frame can rival composite on weight and ride feedback and quality,” Mason continues, noting that modern framesets, such as the brand’s all-road Definition “draw on many of the design influences learnt from composite frames, such as oversized BB’s, taper head tubes and switchable internal routing”.
Aluminium in the pro peloton
When it comes to road bikes ‘light’ is a relative term. In a sport where reducing weight can be an obsession, steel was to be superseded. There were simply lighter materials out there. When Big Mig returned to France in 1995 to defend his crown (successfully so, making it five Tour de France titles for the Spaniard) he did so on an aluminium Pinarello Keral Lite.
But while steel’s reign in the professional peloton was long, aluminium’s was brief. Marco Pantani won the 1998 Tour de France riding a custom Bianchi Mega Pro XL made using Dedacciai doubled-butted 7000-series shaped aluminium tubes. It was more than two kilograms lighter than Indurain’s bike from 1994. However, despite its advancements it would be the last time an alloy bike was ridden to victory in France’s greatest race. From here on, it was carbon that would wear the crown.
Mason, of course, isn't the only brand to utilise aluminium’s strengths. Many of today’s big brands offer aluminium road bike models, often more affordable versions of its high-end carbon bikes, such as Trek’s Émonda ALR, which shares many of the design attributes of the more expensive SL and SLR carbon models. In 2024 Trek merged the Émonda with the Madone, to create one lightweight carbon race bike. So while the carbon Émonda will be phased out, reportedly an aluminium version will still be offered.
However, perhaps an even better indication of aluminium’s performance credentials is the continued development of two of its most iconic framesets, the Cannondale CAAD and the Specialized Allez.
Cannondale has been producing its alloy race bike for almost four decades with the CAAD13 its most recent iteration. It’s a good example of an aluminium bike taking influences from carbon composite frames as Mason notes, with oversize truncated aero tubing, dropped stays and fully integrated cables.
Likewise, Specialized's latest version of the Allez Sprint. demonstrates that brands still aluminium as a viable frame material for racing. It’s a bike that borrows “innovation and insight” from one of its carbon race bikes, the Tarmac SL7, to create what the US brand calls “the world’s fastest alloy road bike.” Over the years it’s a bike that’s gained a reputation in the world of crit riding. Due to the shorter distances of these races, comfort takes a back seat to frame stiffness, which the Allez Sprint, like many alloy race frames, delivers in spades. The higher volume of crashes, due to the frenetic nature of crits, also makes aluminium a smart choice over a pricey carbon frame, another key to the Allez Sprint’s popularity.
To create the aero profiles that are featured on both the CAAD13 and the Allez Sprint, as well as many other alloy race bikes, the tubes are hydroformed into the desired shapes. The tubes are then butted, as with a steel frame these can be double and triple butted, and formed to the desired extent before being welded together.
Most manufacturers use TIG welds, where the same material is used across the frame and welds to create an even join. Ideally, the weld should be smooth - an uneven, bumpy line can be a warning sign of questionable handy work, though some brands may be open about doing this to save money for the consumer. The Allez Sprint’s noticeable welds raised a few eyebrows on its release while Trek uses its Invisible Weld technology to create an almost seamless look that aims to resemble a carbon composite frameset.
As for aluminum’s reputation as delivering a somewhat harsh ride, it’s worth considering Mason’s words regarding tube manipulation and sensible design, two elements that can have a greater effect on ride quality than the material itself; the dropped stays on both the Allez Sprint and the CAAD13 an obvious example of how tube shape and frame design is used to add comfort and compliance to a performance alloy road frame.
Titanium as a road bike frame material
Titanium at a glance
Pros: Superior ride quality, longevity, less commonplace
Cons: Expensive, less choice outside of custom-build options
Who's it best for? Riders who want the benefits of steel in a lighter, stronger package
Titanium as a bike frame material is the most expensive of the three alternatives to carbon. It’s also used less frequently, often the material of choice for the boutique custom frame builder. Much of this is due to the difficulty of working with the material, especially compared to steel or aluminum.
“It is a lot harder to machine, a lot harder to weld and a lot harder to finish than steel” says UK builder Caren Hartley, who had built many a custom frame under the Isen brand name. “We had to essentially build or buy a completely separate set of tooling to work with it, but if you are trying to build the ultimate bike in metal, titanium has to be an option.”
So what makes it such a desirable material for both frame builders and cyclists?
Like steel it possesses that lively, springy feel that makes it both comfortable yet responsive. But it’s also stiffer and lighter, two of the possible drawbacks of a steel frameset. When we asked Hartley about the differences a rider may note between a steel and a titanium frame, weight was mentioned over any particular ride characteristic.
“Different materials will need different choices of tube and possibly frame geometry to achieve the same 'feel'," she says. “The main thing you would be able to notice is the weight of the frame when riding, for example there would be around a 500-700g difference between one of our steel and titanium All Season frames, although both are designed to perform in very similar ways.”
Titanium in the pro peloton
Titanium’s impact in professional road racing is less pronounced. Notoriously difficult to work with, it's better known as a material used by custom frame builders or by brands in limited numbers, often for sportive or endurance frames where comfort is king. That said, Luis Ocana did win the 1973 Tour de France on a British-made Speedwell Titalite, which reportedly weighed 7.8kg, astonishingly light for the time.
Titanium is also incredibly durable. When cyclists talk of finding a ‘bike for life’ titanium's longevity is usually part of the consideration. Mason also builds titanium frames and it is this durability that, in some part, informs the decision to use the material.
“Titanium is the strongest, most impact resistant, most corrosion resistant and lightest material that we make frames from,” says Mason. “A well-crafted titanium frame will last a lifetime as well as being extremely well suited to recycling” - making it a more sustainable choice.
Titanium tubes are usually butted like their steel and aluminum counterparts. When used to create a bike frame, the tubes are alloyed - often with aluminium. Once the tubes have been created and formed, they're welded together - like aluminium, though the process is slightly more drawn out as the sections being welded can't be exposed to oxygen.
“We use the best Titanium tubing available, made by Reynolds and all of the main tubes are triple butted just like their steel tubes,” says Hartley in reference to the Isen range. “This means we can use tubes with some of the thinnest wall thicknesses, and therefore lowest weights achievable in our titanium bikes.”
Certainly if you’re seeking a sublime ride quality then a modern titanium frameset is a great, albeit expensive, place to start. In many ways it's the added expense that has helped make the material so sought after, just like any luxury item.
“It’s very name suggests mythical properties,” says Mason. “Once reserved for the cutting edge aviation, space exploration, formula 1 and medical industry, it’s still the most advanced metal that has been developed for bicycle frame construction.”
Perhaps then we shouldn't be surprised to learn that the No.22 Bicycle Company, which makes handmade Ti frames in the US, has just unveiled a 3D-printed prototype named the Reactor Aero. Dubbed a 'world first', it features an aero-enhanced frame design that's 3D-printed using Grade 5 titanium powder.
The Reactor Aero prototype is 3D-printed using titanium powder
However it’s worth remembering that frame material alone doesn’t make for a superior frameset. The choice of tube, the bike’s geometry and design and the skill of the builder are all vital components that make a modern road bike - whether it be titanium, steel or alumimun - ride well.
“We are slightly wary of the concept of different materials having different ride characteristics,” says Hartley. “ Although obviously different bikes can feel very different to ride, but this is almost always down to things like tube thickness, tube diameter, geometry and so on. “
“For most people, we are trying to find the balance between a bike being able to transfer as much of your power as possible when you're out of the saddle and stamping on the pedals, while not being so stiff that it beats you to death after half an hour.”
Thank you for reading 20 articles this month* Join now for unlimited access
Enjoy your first month for just £1 / $1 / €1
*Read 5 free articles per month without a subscription
Join now for unlimited access
Try first month for just £1 / $1 / €1
The latest race content, interviews, features, reviews and expert buying guides, direct to your inbox!
Luke Friend has worked as a writer, editor and copywriter for over twenty five years. Across books, magazines and websites, he's covered a broad range of topics for a range of clients including Major League Baseball, Golf Digest, the National Trust and the NHS. He has an MA in Professional Writing from Falmouth University and is a qualified bicycle mechanic. He has been a cycling enthusiast from an early age, partly due to watching the Tour de France on TV. He's a keen follower of bike racing to this day as well as a regular road and gravel rider.